In der heutigen Fertigungswelt ist die CNC-Bearbeitungstechnologie aufgrund ihrer hohen Präzision und Wiederholgenauigkeit zu einem integralen Bestandteil des Fertigungsprozesses geworden.Um jedoch die Vorteile der CNC-Technologie voll ausschöpfen zu können, ist die Sicherstellung der Produktqualität von entscheidender Bedeutung.Die Qualitätskontrolle spielt in der CNC-Fertigung eine zentrale Rolle und wirkt sich direkt auf die Produktionseffizienz, die Kosten sowie die Leistung und Zuverlässigkeit des Endprodukts aus.In diesem Artikel wird untersucht, wie eine effektive Qualitätskontrolle im CNC-Fertigungsprozess erreicht werden kann.
Teil 1: Die Grundkonzepte der Qualitätskontrolle in der CNC-Bearbeitung
Die Qualitätskontrolle umfasst als eine Reihe systematischer Prozesse und Maßnahmen, um sicherzustellen, dass Produkte den erforderlichen Qualitätsstandards entsprechen, die gesamte Produktionskette von der Rohstoffauswahl bis zur endgültigen Produktlieferung.Dieses Konzept ist besonders wichtig in der CNC-Fertigungsumgebung, da jeder kleine Fehler zu viel Ausschuss und Produktfehlern führen kann.Daher besteht das Ziel der Qualitätskontrolle nicht nur darin, die Produktqualifizierungsrate zu maximieren, sondern auch die Kosten durch Reduzierung von Ausschuss und Nacharbeit zu senken und gleichzeitig die Kundenzufriedenheit und Wettbewerbsfähigkeit auf dem Markt zu verbessern.
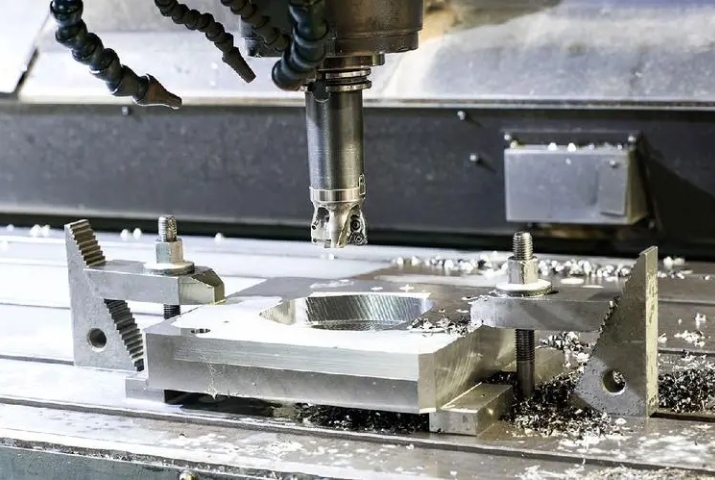
Teil II: Schlüsselstrategien und Techniken der Qualitätskontrolle in der CNC-Bearbeitung
1. Auswahl und Wartung von Ausrüstung und Werkzeugen
Die Auswahl von CNC-Maschinen und -Werkzeugen, die für spezifische Fertigungsanforderungen geeignet sind, ist für die Qualitätssicherung von entscheidender Bedeutung.Hochwertige Geräte können Schneid- und Formaufgaben präziser und mit weniger Ausfällen ausführen.Darüber hinaus sind regelmäßige Wartung und Kalibrierung von entscheidender Bedeutung, um die langfristige Stabilität und Genauigkeit der Geräte sicherzustellen.Durch die Auswahl der richtigen Maschinen und Werkzeuge kann nicht nur die Verarbeitungseffizienz verbessert, sondern auch die Lebensdauer der Ausrüstung verlängert und die Betriebskosten langfristig gesenkt werden.
2. Bedienerschulung und -management
Für die Qualitätskontrolle sind hochqualifizierte Bediener unerlässlich.Durch Investitionen in eine systematische Schulung und kontinuierliche Weiterbildung der Mitarbeiter können die betriebliche Genauigkeit und Effizienz erheblich verbessert und die Fehlerquote gesenkt werden.Durch regelmäßige Schulungen und Beurteilungen werden die Mitarbeiter über die neueste CNC-Technologie auf dem Laufenden gehalten und stellen sicher, dass ihre Abläufe den höchsten Industriestandards entsprechen
3. Programmverifizierung und Simulation
Vor dem offiziellen Produktionsstart können durch Programmverifizierung und Simulation potenzielle Fehler vermieden werden.Der Einsatz fortschrittlicher CAD/CAM-Software kann dabei helfen, mögliche Fehler im Design zu erkennen und sie vor der Produktion zu korrigieren.Dadurch wird nicht nur die Produktionseffizienz verbessert, sondern auch die Produktkonsistenz und -qualität sichergestellt.
4. Materialauswahl und -management
Die Auswahl der richtigen Materialien und die Sicherstellung ihrer Qualität sind die Grundlage für die Qualität des Endprodukts.Gleichzeitig kann ein angemessenes Materialverwaltungs- und -verfolgungssystem sicherstellen, dass jede verwendete Materialcharge den Standards entspricht.Die Konsistenz und Qualität der Materialien wirken sich direkt auf die Leistung des Endprodukts aus. Daher ist ein strenges Materialauswahl- und Managementsystem unerlässlich.
5. Umweltkontrolle
Die Umgebungsbedingungen, in denen sich die CNC-Maschine befindet, wie Temperatur und Luftfeuchtigkeit, wirken sich auf die Bearbeitungsgenauigkeit aus.Daher ist die Aufrechterhaltung einer stabilen Produktionsumgebung für die Gewährleistung der Produktqualität von entscheidender Bedeutung.Durch die Kontrolle dieser Variablen können durch Umweltfaktoren verursachte Qualitätsprobleme reduziert werden.
6. Verbessern Sie das Qualitätssystem
Stärkung der Qualitätssicherungsmaßnahmen im Produktionsprozess, Verbesserung der Stabilität der Prozessqualität und Gewährleistung der effektiven Umsetzung von Qualitätsfunktionen in allen Gliedern des Produktionsprozesses.Fördern Sie das Qualitätsüberwachungssystem und implementieren Sie den Belohnungs- und Bestrafungsmechanismus, um sicherzustellen, dass jeder Link den Qualitätsstandards entspricht, und ermutigen Sie die Mitarbeiter, auf die Produktqualität zu achten und diese zu verbessern.
7. Drei-Koordinaten-Messung
Durch die Drei-Koordinaten-Messung ist es möglich, genau zu bestimmen, ob der Fehler des Werkstücks innerhalb des zulässigen Toleranzbereichs liegt, wodurch Produktausfälle aufgrund übermäßiger Fehler vermieden werden.Basierend auf den präzisen Daten der Drei-Koordinaten-Messung können Produktionsmitarbeiter die Verarbeitungstechnologie anpassen, Produktionsparameter optimieren und Abweichungen in der Produktion reduzieren.Gleichzeitig kann ein Drei-Koordinaten-Messgerät eine Vielzahl herkömmlicher Oberflächenmessgeräte und teurer Kombinationsmessgeräte ersetzen, die Messgeräte vereinfachen und die Messeffizienz verbessern.
GPM wurde 2004 gegründet und ist ein professioneller Hersteller von Präzisionsmaschinenteilen.Das Unternehmen hat viel Geld investiert, um importierte High-End-Hardware einzuführen.Durch sorgfältige Konstruktion und Wartung, professionelle Bedienerschulung, präzise Programmüberprüfung, Echtzeit-Produktionsüberwachung und hervorragende Materialien wird eine wirksame Qualitätskontrolle im Herstellungsprozess gewährleistet.Das Unternehmen verfügt über ISO9001-, ISO13485-, ISO14001- und andere Systemzertifizierungen sowie über die deutsche Drei-Koordinaten-Inspektionsausrüstung von Zeiss und stellt so sicher, dass sich das Unternehmen im Produktions- und Managementprozess strikt an internationale Standards hält.
Zeitpunkt der Veröffentlichung: 29. Juni 2024