Koneiden valmistuksen alalla laatikkoosat ovat yleinen rakenneosien tyyppi, ja niitä käytetään laajalti erilaisissa mekaanisissa laitteissa.Monimutkaisen rakenteensa ja korkeiden tarkkuusvaatimustensa vuoksi laatikkoosien käsittelytekniikka on erityisen kriittinen.Tämä artikkeli selittää kattavasti ja ammattimaisesti laatikon osien käsittelytekniikan auttaakseen lukijoita ymmärtämään ja hallitsemaan asiaankuuluvaa tietoa paremmin.
Sisältö:
Osa 1. Laatikon osien rakenteelliset ominaisuudet
Osa 2. Laatikon osien käsittelyvaatimukset
Osa 3. Laatikon osien tarkkuustyöstö
Osa 4. Laatikon osien tarkastus
1. Laatikon osien rakenteelliset ominaisuudet
Monimutkaiset geometriset muodot
Laatikon osat koostuvat yleensä useista pinnoista, rei'istä, rakeista ja muista rakenteista, ja sisäpuoli voi olla ontelomainen, ohuita ja epätasaisia seiniä.Tämä monimutkainen rakenne edellyttää monien näkökohtien tarkkaa hallintaa laatikon osien suunnittelu- ja valmistusprosessin aikana.
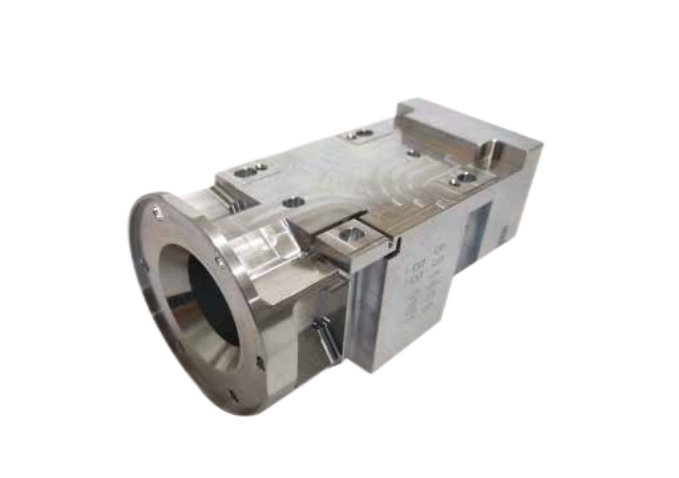
Korkeat tarkkuusvaatimukset
Laatikon osien prosessointi ei edellytä ainoastaan kunkin pinnan yhdensuuntaisuutta ja kohtisuoraa suunnitteluvaatimusten täyttämiseksi, vaan siihen liittyy myös reikien asennon tarkkuus.Nämä ovat avaintekijöitä laatikon osien normaalin toiminnan varmistamiseksi.
Materiaalin ominaisuudet
Laatikon osissa yleisesti käytetyt materiaalit ovat valurautaa tai valuterästä.Näiden materiaalien leikkausteho on suhteellisen huono, mikä lisää käsittelyn vaikeutta.
2. Laatikon osien käsittelyvaatimukset
Varmista mittojen ja muodon tarkkuus
Laatikon osien käsittelyn aikana koon ja muodon tarkkuutta on valvottava tiukasti kokoonpano- ja käyttövaatimusten täyttämiseksi.
Asennon tarkkuus
Reikien asennon tarkkuus on erityisen tärkeä laatikkoosille, koska reikien asemien tarkkuus on suoraan verrannollinen koko mekaanisen järjestelmän toimintatarkkuuteen ja vakauteen.
Pinnan karheus
Laatikon osien kosketusjäykkyyden ja keskinäisen asennontarkkuuden varmistamiseksi päätasojen muototarkkuuden ja pinnan karheuden on saavutettava korkeammat standardit.
Jatkokäsittely
Itse koneistuksen lisäksi laatikon osille on suoritettava myös useita myöhempiä käsittelyjä käsittelyn päätyttyä, kuten puhdistus, ruosteenesto ja maalaus niiden ulkonäön laadun ja kestävyyden parantamiseksi.
Laatikon osien tarkkuustyöstö
Laatikon osien viimeistely on erittäin suurta tarkkuutta vaativa prosessi, joka liittyy suoraan koko mekaanisen järjestelmän kokoonpanon laatuun ja suorituskykyyn.Laatikon osien viimeistelyssä on kiinnitettävä erityistä huomiota seuraaviin asioihin:
Koneiden ja työkalujen valinta
Korkean tarkkuuden työstötulosten saavuttamiseksi on käytettävä erittäin tarkkoja työstökoneita ja leikkaustyökaluja.Tämä sisältää, mutta ei rajoittuen, tehokkaat laitteet, kuten CNC-pystysorvit, CNC-pystytyöstökeskukset ja vaakasuuntaiset työstökeskukset sekä korkean tarkkuuden työkalut, jotka on tarkoitettu laatikon viimeistelyyn.
Prosessointiparametrien optimointi
Viimeistelyprosessin aikana parametreja, kuten leikkausnopeutta ja syöttönopeutta, on säädettävä tarkasti.Liian korkeat tai liian alhaiset parametriasetukset voivat vaikuttaa käsittelyn laatuun, kuten aiheuttaa liiallisia leikkausvoimia, jotka aiheuttavat osan muodonmuutoksia, tai käsittelyteho on liian alhainen.
Lämpötilan ja muodonmuutosten hallinta
Viimeistelyprosessin aikana pitkästä jatkuvasta leikkausajasta johtuen ylikuumeneminen on helppoa, mikä johtaa epätarkkoihin osien mittoihin tai huonontuneeseen pinnan laatuun.Siksi on ryhdyttävä toimenpiteisiin, kuten jäähdytysnesteen käyttö, käsittelyjärjestyksen ja lepoajan järkevä järjestäminen lämpötilan hallitsemiseksi ja lämpömuodonmuutosten vähentämiseksi.
Reiän työstön tarkkuus
Kotelo-osien reikien käsittely on erityistä huomiota vaativa osa, erityisesti erittäin korkeaa asennontarkkuutta ja koaksiaalisuutta vaativissa rei'issä.Reikien mittatarkkuuden ja pinnan laadun varmistamiseksi tulee käyttää porausta, kalvinta, kalvinta ja muita menetelmiä.Samalla tulee kiinnittää huomiota reikien väliseen sijaintisuhteeseen poikkeamien välttämiseksi.
Työkappaleen kiinnitysmenetelmä
Oikea kiinnitysmenetelmä on ratkaisevan tärkeä käsittelytarkkuuden varmistamiseksi.Asianmukaiset työkalut tulee suunnitella varmistamaan työkappaleen vakaus käsittelyn aikana ja välttämään virheellisen kiinnityksen aiheuttamat käsittelyvirheet.Esimerkiksi siirtymäkierrereikien menetelmällä voidaan suorittaa suurten pintojen jyrsiminen ja poraus yhdellä kiinnityksellä, mikä parantaa tehokkaasti tasaisuutta.
4. Laatikon osien tarkastus
Laatikon osien tarkastus on keskeinen vaihe sen varmistamiseksi, että ne täyttävät mekaanisen järjestelmän tarkkuus- ja suorituskykyvaatimukset.Tarkastusprosessin aikana on kiinnitettävä huomiota moniin yksityiskohtiin.
Mittausvälineet
Korkean tarkkuuden mittaustulosten saavuttamiseksi on tarpeen käyttää erittäin vakaita ja tehokkaita mittaustyökaluja, kuten kolmiulotteisia koordinaattimittauskoneita.Näillä laitteilla voidaan saada sarja tarkkoja mittauksia laatikon osien mitoista, tasaisuudesta, koaksiaalisuudesta jne.
Määritä mittaustarvikkeet
Mittaukset syvissä reikissä ja onteloissa vaativat sopivat jatkotangot ja kynät, kuten testipohjan jatkotangot, tähden muotoiset kynät jne. mittaustarkkuuden varmistamiseksi.
Määritä sijainti
Ennen mittaamista on tarpeen selvittää laatikon osien sijoitustapa.Yleisesti käytetään kolmea keskenään kohtisuoraa pintaa asemointia varten tai tasoa, jossa on kaksi kohtisuoraa reikää asemointia varten.Tämä auttaa parantamaan mittauksen toistettavuutta ja vakautta.
Harkitse asennusmenetelmiä
Ottaen huomioon, että laatikon osat ovat kooltaan suhteellisen suuria ja painoltaan raskaita, on kiinnityksen yhteydessä varmistettava mukavuus, toistettavuus ja vakaus.Ne voidaan sijoittaa suoraan työtasolle mittausta varten tai ne voidaan kiinnittää yleiskiinnikkeillä tai yksinkertaisilla puristimilla.
Noudata varotoimia
Mittauksen aikana tulee varmistaa, että osat on pyyhitty puhtaiksi ja purseettomiksi, pitää mittauselementtien pintatarkkuus korkeana ja valita sopiva mittausnopeus osien virheellisen liikkeen välttämiseksi, varsinkin jos kokoja on useita.Samanaikaisesti paikoissa, joita on vaikea mitata suoraan, voidaan harkita useita kiinnitys- tai epäsuoria mittausmenetelmiä.
Analysoi mittaustiedot
Mittaustiedot on analysoitava huolellisesti, erityisesti keskeiset parametrit, kuten reiän mittatarkkuus, sylinterimäisyys ja koaksiaalisuus, jotka on analysoitava todellisten käsittely- ja kokoonpanoolosuhteiden yhteydessä mittaustulosten tarkkuuden ja luotettavuuden varmistamiseksi.
Vahvista mittaustaidot
Kun mittaat reiän akselia, voit ensin mitata pinnan, joka on kohtisuorassa reikään nähden ja sitten syöttää pinnan vektorisuunta automaattisen ympyrän (sylinterin) mittauksen vektorisuuntaan olettaen, että reikä on teoreettisesti kohtisuorassa reiän kanssa. pinta.Mittattaessa kohtisuoraa reiän akselin pituuden ja pinnan suhteellinen suhde on arvioitava kokemuksen perusteella.Jos reiän syvyys on suhteellisen matala ja pinta on suhteellisen suuri, ja reikä on vertailukohtana, tulos voi olla toleranssin ulkopuolella (itse asiassa se on hyvä).Voit harkita mittaamista reikään työnnetyllä karalla tai mittaamista kahdella reiällä, jotka jakavat yhteisen akselin.
GPM:llä on 20 vuoden kokemus erilaisten tarkkuusosien CNC-työstyksestä.Olemme työskennelleet asiakkaiden kanssa monilla teollisuudenaloilla, mukaan lukien puolijohteet, lääketieteelliset laitteet jne., ja olemme sitoutuneet tarjoamaan asiakkaille laadukkaita ja tarkkoja koneistuspalveluita.Otamme käyttöön tiukan laadunhallintajärjestelmän varmistaaksemme, että jokainen osa vastaa asiakkaiden odotuksia ja standardeja.
Tekijänoikeushuomautus:
GPM Intelligent Technology(Guangdong) Co., Ltd. advocates respect and protection of intellectual property rights and indicates the source of articles with clear sources. If you find that there are copyright or other problems in the content of this website, please contact us to deal with it. Contact information: marketing01@gpmcn.com
Postitusaika: 27.5.2024