ပလတ်စတစ်အမှုန်အမွှားများကို ပလပ်စတစ်ထုတ်ကုန်များအဖြစ်သို့ ပြောင်းလဲပုံသွင်းခြင်းလုပ်ငန်းစဉ်တွင်၊ ပလတ်စတစ်များသည် မကြာခဏဆိုသလို မြင့်မားသော အပူချိန်နှင့် ဖိအားများကို ခံကြရပြီး မြင့်မားသော ရှွန်းမှုနှုန်းဖြင့် စီးဆင်းသွားကြသည်။မတူညီသော ပုံသွင်းမှုအခြေအနေများနှင့် လုပ်ငန်းစဉ်များသည် ထုတ်ကုန်အရည်အသွေးအပေါ် ကွဲပြားခြားနားသောအကျိုးသက်ရောက်မှုများရှိမည်ဖြစ်သည်။ဆေးထိုးပုံသွင်းခြင်းတွင် ပလတ်စတစ်ပါ၀င်သည် ၊ ကုန်ကြမ်း၊ ဆေးထိုးစက်၊ မှိုနှင့် ဆေးထိုးခြင်းလုပ်ငန်းစဉ် လေးမျိုးပါဝင်သည်။
ထုတ်ကုန်များ၏ အရည်အသွေးတွင် အတွင်းပစ္စည်း အရည်အသွေးနှင့် အသွင်အပြင် အရည်အသွေးတို့ ပါဝင်သည်။အတွင်းပိုင်းပစ္စည်း အရည်အသွေးသည် အဓိကအားဖြင့် စက်ပိုင်းဆိုင်ရာ ခွန်အားဖြစ်ပြီး၊ အတွင်းစိတ်ဖိစီးမှု အရွယ်အစားသည် ထုတ်ကုန်၏ စက်ပိုင်းဆိုင်ရာ ခိုင်ခံ့မှုကို တိုက်ရိုက် သက်ရောက်မှုရှိသည်။အတွင်းစိတ်ဖိစီးမှုကို ဖြစ်ပေါ်စေသည့် အဓိကအကြောင်းရင်းများကို ပလပ်စတစ်ပုံသွင်းခြင်းတွင် မော်လီကျူးများ၏ ပုံဆောင်ခဲများ နှင့် မော်လီကျူးများ၏ တိမ်းညွှတ်မှုတို့ကြောင့် ဆုံးဖြတ်သည်။၏ထုတ်ကုန်၏ အသွင်အပြင် အရည်အသွေးသည် ထုတ်ကုန်၏ မျက်နှာပြင် အရည်အသွေးဖြစ်သော်လည်း ကြီးမားသော အတွင်းစိတ်ဖိစီးမှုကြောင့် ဖြစ်ပေါ်လာသော ထုတ်ကုန်၏ ကွဲထွက်ခြင်းနှင့် ပုံပျက်ခြင်းတို့သည် အသွင်အပြင် အရည်အသွေးကို ထိခိုက်စေပါသည်။ထုတ်ကုန်များ၏ ပုံပန်းသဏ္ဍာန် အရည်အသွေးတွင်- မလုံလောက်သော ထုတ်ကုန်များ၊ ထုတ်ကုန်အစွန်းများ၊ ဂွမ်းအမှတ်အသားများ၊ ဖလက်ရှ်၊ ပူဖောင်းများ၊ ငွေဝါယာကြိုးများ၊ အနက်ရောင်အစက်အပြောက်များ၊ ပုံပျက်ခြင်း၊ အက်ကွဲခြင်း၊ ကွဲထွက်ခြင်း၊ အခွံခွာခြင်းနှင့် အရောင်ပြောင်းခြင်း စသည်ဖြင့်၊ ပုံသွင်းခြင်းဆိုင်ရာ အပူချိန်၊ ဖိအား၊ စီးဆင်းမှု၊ အချိန်၊ နှင့်ရာထူး။ဆက်စပ်။
အကြောင်းအရာ
အပိုင်းတစ်- ပုံသွင်းအပူချိန်
အပိုင်းနှစ်- ပုံသွင်းခြင်းလုပ်ငန်းစဉ်ဖိအား
အပိုင်းသုံး- ဆေးထိုးပုံသွင်းစက် အရှိန်
အပိုင်းလေး- အချိန်သတ်မှတ်ခြင်း။
အပိုင်းငါး- ရာထူးထိန်းချုပ်မှု
အပိုင်းတစ်- ပုံသွင်းအပူချိန်
စည်အပူချိန်၎င်းသည် ပလပ်စတစ်၏ အရည်ပျော်သည့် အပူချိန်ဖြစ်သည်။စည်၏ အပူချိန်သည် မြင့်မားနေပါက အရည်ပျော်ပြီးနောက် ပလပ်စတစ်၏ ပျစ်ဆိမ့်မှု နည်းပါးသည်။တူညီသောထိုးဆေးဖိအားနှင့် စီးဆင်းမှုနှုန်းအောက်တွင်၊ ဆေးထိုးသည့်အမြန်နှုန်းသည် မြန်သည်၊ ပုံသွင်းထားသောထုတ်ကုန်များသည် flash၊ ငွေရောင်၊ အရောင်ပြောင်းခြင်းနှင့် ကြွပ်ဆတ်မှု ဖြစ်နိုင်သည်။
စည်၏အပူချိန်အလွန်နိမ့်သည်၊ ပလပ်စတစ်သည်ညံ့ဖျင်းသောပလပ်စတစ်ပြုလုပ်ထားသော၊ viscosity မြင့်မားသည်၊ ဆေးထိုးနှုန်းသည်တူညီသောထိုးသွင်းဖိအားနှင့်စီးဆင်းမှုနှုန်းအောက်တွင်နှေးကွေးသည်၊ ပုံသွင်းထားသောထုတ်ကုန်များသည်လွယ်ကူစွာမလုံလောက်ပါ၊ ဂွမ်းအမှတ်များသည်ထင်ရှားသည်၊ အတိုင်းအတာများဖြစ်သည်။ မတည်မငြိမ်ဖြစ်ပြီး ထုတ်ကုန်များတွင် အအေးတုံးများရှိသည်။
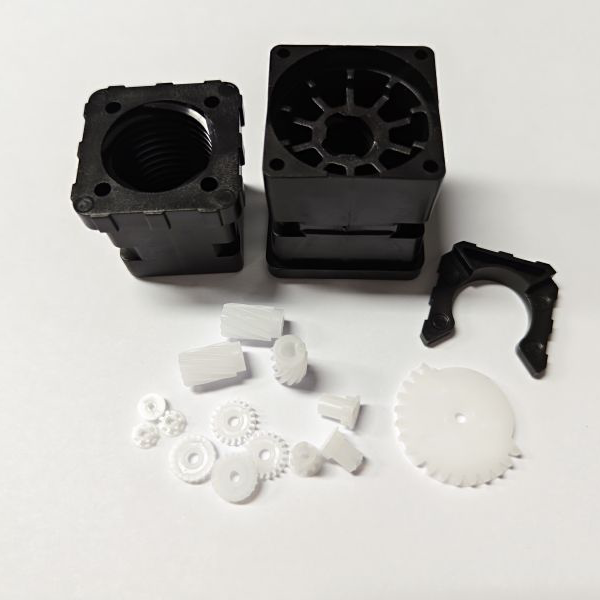
Nozzle အပူချိန်နော်ဇယ်အပူချိန်ကို မြင့်မားစွာသတ်မှတ်ထားပါက၊ နော်ဇယ်သည် ထုတ်ကုန်အတွင်းရှိ အေးသောအမျှင်များကို ဖြစ်ပေါ်စေပြီး အလွယ်တကူ ယိုစိမ့်သွားမည်ဖြစ်သည်။အပူချိန်နိမ့်သော နော်ဇယ်သည် မှိုလောင်းခြင်းစနစ်၏ ပိတ်ဆို့ခြင်းကို ဖြစ်စေသည်။ပလပ်စတစ်ထိုးသွင်းရန် ဆေးထိုးဖိအားကို တိုးပေးရမည်ဖြစ်သော်လည်း ပုံသွင်းထားသော ထုတ်ကုန်တွင် အအေးဓာတ် ချက်ချင်းရှိနေမည်ဖြစ်သည်။
မှိုအပူချိန်မှိုအပူချိန်မြင့်မားပါက ဆေးထိုးဖိအားနှင့် စီးဆင်းမှုနှုန်းကို လျှော့ချနိုင်သည်။သို့သော်လည်း တူညီသောဖိအားနှင့် စီးဆင်းမှုနှုန်းတွင်၊ ထုတ်ကုန်သည် လွယ်ကူစွာ ဖျတ်ခနဲ၊ ကွဲထွက်ပြီး ပုံပျက်သွားမည်ဖြစ်ပြီး ထုတ်ကုန်ကို ပုံစံခွက်မှ ထုတ်ပစ်ရန် ခက်ခဲမည်ဖြစ်သည်။မှိုအပူချိန်သည် နိမ့်နေပြီး တူညီသော ဆေးထိုးဖိအားနှင့် စီးဆင်းမှုနှုန်းအောက်တွင်၊ ထုတ်ကုန်သည် ပူဖောင်းများနှင့် ဂဟေဆက်မှုအမှတ်အသားများ စသည်တို့ဖြင့် မလုံလောက်ဘဲ ဖွဲ့စည်းထားပါသည်။
ပလပ်စတစ်အခြောက်ခံအပူချိန်အမျိုးမျိုးသော ပလတ်စတစ်များသည် ခြောက်သွေ့သောအပူချိန် အမျိုးမျိုးရှိသည်။ABS ပလတ်စတစ်များသည် ယေဘူယျအားဖြင့် အခြောက်ခံအပူချိန် 80 မှ 90°C ကိုသတ်မှတ်ထားသောကြောင့် အစိုဓာတ်နှင့်ကျန်ရှိသောပျော်ရည်များကို အခြောက်ခံရန်ခက်ခဲပြီး ထုတ်ကုန်များတွင် ငွေဝါယာကြိုးများနှင့် ပူဖောင်းများ အလွယ်တကူရရှိနိုင်ပြီး ထုတ်ကုန်များ၏ ကြံ့ခိုင်မှုလည်း လျော့နည်းသွားမည်ဖြစ်သည်။
အပိုင်းနှစ်- ပုံသွင်းခြင်းလုပ်ငန်းစဉ်ဖိအား
ကြိုတင်ပုံသွင်းထားသော နောက်ကျောဖိအား-high back pressure နှင့် high storage density ဆိုသည်မှာ တူညီသော storage volume အတွင်းတွင် နောက်ထပ် ပစ္စည်းများကို သိမ်းဆည်းနိုင်သည်။Low back pressure ဆိုသည်မှာ သိုလှောင်မှုသိပ်သည်းဆနည်းပြီး သိုလှောင်မှုနည်းသော ပစ္စည်းကို ဆိုလိုသည်။သိုလှောင်မှု အနေအထားကို သတ်မှတ်ပြီးနောက်၊ နောက်ကျောဖိအားကို ကြီးမားသော ချိန်ညှိမှု ပြုလုပ်ပြီးနောက်၊ သိုလှောင်မှု အနေအထားကို ပြန်လည်သတ်မှတ်ရန် အာရုံစိုက်ရမည်၊ မဟုတ်ပါက ဖလက်ရှ် သို့မဟုတ် ထုတ်ကုန် မလုံလောက်မှုကို အလွယ်တကူ ဖြစ်စေနိုင်သည်။
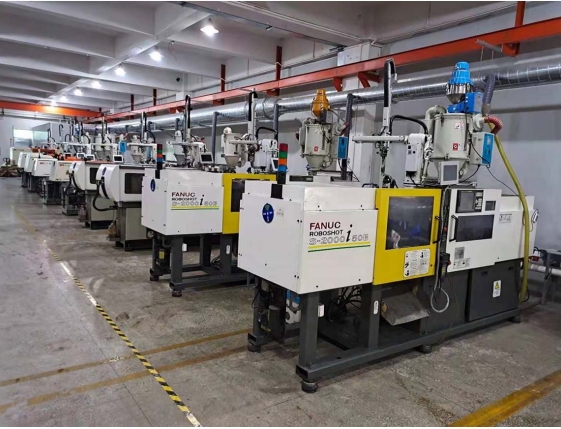
ထိုးသွင်းဖိအား-ပလတ်စတစ် အမျိုးအစား အမျိုးမျိုးတွင် အရည်ပျော် viscosity အမျိုးမျိုးရှိသည်။Amorphous ပလတ်စတစ်များ၏ ပျစ်ပျစ်နိုင်မှုမှာ ပလတ်စတစ်ပြုလုပ်ခြင်း၏ အပူချိန်ပြောင်းလဲမှုနှင့်အတူ အလွန်ပြောင်းလဲသွားသည်။ဆေးထိုးဖိအားကို ပလပ်စတစ်၏ ဂဟေဆက်ခြင်း၏ viscosity နှင့် plastic process ratio အရ သတ်မှတ်ထားသည်။ဆေးထိုးဖိအားကို သတ်မှတ်သတ်မှတ်ထားလျှင် အလွန်နိမ့်ပါက၊ ထုတ်ကုန်သည် လုံလောက်စွာ ထိုးသွင်းခံရမည်ဖြစ်ပြီး အစွန်းအထင်းများ၊ ဂဟေသားအမှတ်အသားများနှင့် မတည်မငြိမ်ဖြစ်သော အတိုင်းအတာများ ဖြစ်ပေါ်စေမည်ဖြစ်သည်။ဆေးထိုးဖိအားများလွန်းပါက၊ ထုတ်ကုန်သည် ဖလက်ရှ်၊ အရောင်ပြောင်းခြင်းနှင့် မှိုထုတ်ရာတွင် ခက်ခဲခြင်းရှိမည်။
Clamping ဖိအား-၎င်းသည် မှိုအပေါက်၏ ခန့်မှန်းဧရိယာနှင့် ဆေးထိုးဖိအားအပေါ် မူတည်သည်။Clamping Pressure မလုံလောက်ပါက၊ ထုတ်ကုန်သည် လွယ်ကူစွာ မီးတောက်လာပြီး အလေးချိန်တိုးလာပါမည်။ကုပ်ကြိုးက အရမ်းကြီးနေရင် မှိုကိုဖွင့်ရခက်လိမ့်မယ်။ယေဘူယျအားဖြင့်၊ clamping pressure setting သည် 120par/cm2 ထက်မပိုသင့်ပါ။
ဖိအားများ-ဆေးထိုးပြီးသောအခါ၊ ဝက်အူအား ဖိထားသောဖိအားဟုခေါ်သော ဖိအားကို ဆက်လက်ပေးသည်။ယခုအချိန်တွင် မှိုပေါက်အတွင်းရှိ ထုတ်ကုန်သည် အေးခဲခြင်းမရှိသေးပါ။ဖိအားကိုထိန်းထားခြင်းဖြင့် ထုတ်ကုန်ပြည့်သွားကြောင်း သေချာစေရန် မှိုပေါက်ကို ဖြည့်ပေးနိုင်သည်။ဖိအားနှင့် ဖိအားဆက်တင်သည် မြင့်မားနေပါက၊ ၎င်းသည် ပံ့ပိုးမှုမှိုနှင့် ဆွဲထုတ်သည့် core ကို ကြီးမားသော ခုခံမှုကို ဆောင်ကျဉ်းပေးလိမ့်မည်။ထုတ်ကုန်သည် အလွယ်တကူ ဖြူပြီး ပျော့သွားလိမ့်မည်။ထို့အပြင်၊ မှိုအပြေးသမားတံခါးအား ဖြည့်စွက်ပလပ်စတစ်ဖြင့် အလွယ်တကူ ချဲ့ထွင်ပြီး တင်းကျပ်မည်ဖြစ်ပြီး အပြေးသမား၏ တံခါးသည် ကျိုးသွားမည်ဖြစ်သည်။ဖိအားနည်းလွန်းပါက၊ ထုတ်ကုန်သည် အစွန်းအထင်းများနှင့် မတည်ငြိမ်သောအတိုင်းအတာများ ရှိလိမ့်မည်။
ထုတ်ယူခြင်းနှင့် နျူထရွန်ဖိအားကို သတ်မှတ်ခြင်း၏ နိယာမမှာ မှိုအပေါက်၏ အကျယ်အဝန်း အရွယ်အစား၊ ထည့်သွင်းထားသော အူတိုင်၏ ပင်မပုံသွင်းဧရိယာနှင့် ပုံသွင်းထုတ်ကုန်၏ ဂျီဩမေတြီ ရှုပ်ထွေးမှုအပေါ် အခြေခံ၍ ဖိအားကို သတ်မှတ်ရန် ဖြစ်သည်။အရွယ်အစား။ယေဘူယျအားဖြင့်၊ ၎င်းသည် ထုတ်ကုန်ကို တွန်းထုတ်နိုင်ရန် အထောက်အပံ့ပေးသောမှိုနှင့် နျူထရွန်ဆလင်ဒါ၏ ဖိအားကို သတ်မှတ်ရန် လိုအပ်သည်။
အပိုင်းသုံး- ဆေးထိုးပုံသွင်းစက် အရှိန်
ဝက်အူအမြန်နှုန်း: ပလတ်စတစ်အကြိုစီးဆင်းမှုနှုန်းကို ချိန်ညှိခြင်းအပြင်၊ ၎င်းသည် အဓိကအားဖြင့် ပလတ်စတစ်အကြိုဖိအားကြောင့် ထိခိုက်ပါသည်။မထည့်ခင် မှိုစီးဆင်းမှုနှုန်းကို ကြီးမားသောတန်ဖိုးနှင့် ချိန်ညှိထားလျှင် ဝက်အူလှည့်သည်နှင့်အမျှ ပလပ်စတစ်သည် ကြီးမားသော ပွတ်တိုက်အားရှိမည်ဖြစ်ပြီး ပလပ်စတစ်မော်လီကျူးဖွဲ့စည်းပုံမှာ အလွယ်တကူ ဖြတ်တောက်နိုင်မည်ဖြစ်သည်။ .ထုတ်ကုန်တွင် အနက်ရောင်အစက်အပြောက်များနှင့် အနက်ရောင်အစင်းကြောင်းများ ပါရှိမည်ဖြစ်ပြီး ထုတ်ကုန်၏ အသွင်အပြင် အရည်အသွေးနှင့် ခိုင်ခံ့မှုကို ထိခိုက်စေမည်ဖြစ်သည်။, နှင့်စည်အပူအပူချိန်ကိုထိန်းချုပ်ရန်ခက်ခဲသည်။အကယ်၍ ပလပ်စတစ်ကြိုတင်စီးဆင်းမှုနှုန်းသည် အလွန်နိမ့်နေပါက၊ ပလပ်စတစ်ကြိုတင်သိုလှောင်မှုအချိန်ကို သက်တမ်းတိုးမည်ဖြစ်ပြီး၊ ၎င်းသည် ပုံသွင်းခြင်းစက်ဝန်းကို ထိခိုက်စေမည်ဖြစ်သည်။
ထိုးနှံမှုအရှိန်-ဆေးထိုးအမြန်နှုန်းကို ကျိုးကြောင်းဆီလျော်စွာ သတ်မှတ်ရမည်ဖြစ်ပြီး၊ မဟုတ်ပါက ထုတ်ကုန်အရည်အသွေးကို ထိခိုက်စေမည်ဖြစ်သည်။ဆေးထိုးအမြန်နှုန်း မြန်လွန်းပါက၊ ထုတ်ကုန်တွင် ပူဖောင်းများ လောင်ကျွမ်းခြင်း၊ အရောင်ပြောင်းခြင်း စသည်ဖြင့် ရှိလာပါမည်။ ဆေးထိုးသည့် အရှိန်သည် နှေးလွန်းပါက၊ ထုတ်ကုန်သည် မလုံလောက်ဘဲ ဖွဲ့စည်းပြီး ဂဟေဆက်သည့် အမှတ်အသားများ ရှိနေပါမည်။
မှိုနှင့် နျူထရွန် စီးဆင်းမှုနှုန်းကို ပံ့ပိုးသည်-မြင့်မားလွန်းသည်ဟု မသတ်မှတ်သင့်ပါ၊ သို့မဟုတ်ပါက ထုတ်လွှတ်ခြင်းနှင့် အူတိုင်ဆွဲခြင်း လှုပ်ရှားမှုများသည် မြန်ဆန်လွန်းသဖြင့် မတည်မငြိမ်ဖြစ်ပြီး ထုတ်လွှတ်ခြင်းနှင့် အူတိုင်ဆွဲခြင်းတို့ကို ဖြစ်ပေါ်စေပြီး ထုတ်ကုန်သည် အလွယ်တကူ အဖြူရောင်သို့ ပြောင်းလဲသွားမည်ဖြစ်သည်။
အပိုင်းလေး- အချိန်သတ်မှတ်ခြင်း။
အခြောက်ခံချိန်-ပလတ်စတစ်ကုန်ကြမ်းများအတွက် အခြောက်ခံချိန်ဖြစ်သည်။ပလတ်စတစ် အမျိုးအစား အမျိုးမျိုးတွင် အကောင်းဆုံး အခြောက်ခံသည့် အပူချိန်နှင့် အချိန်များ ရှိသည်။ABS ပလပ်စတစ်၏ အခြောက်ခံအပူချိန်မှာ 80 ~ 90 ℃ ဖြစ်ပြီး အခြောက်ခံချိန်သည် 2 နာရီဖြစ်သည်။ABS ပလပ်စတစ်သည် ယေဘူယျအားဖြင့် 0.2 မှ 0.4% ရေကို 24 နာရီအတွင်း စုပ်ယူနိုင်ပြီး ဆေးထိုးပုံသွင်းနိုင်သော ရေပါဝင်မှုမှာ 0.1 မှ 0.2% ဖြစ်သည်။
ဆေးထိုးခြင်းနှင့် ဖိအားထိန်းထားချိန်-ကွန်ပြူတာဆေးထိုးစက်၏ ထိန်းချုပ်မှုနည်းလမ်းတွင် ဖိအား၊ အမြန်နှုန်းနှင့် ဆေးထိုးပလပ်စတစ်ပမာဏကို အဆင့်ဆင့်ချိန်ညှိရန် multi-stage injection တပ်ဆင်ထားသည်။မှိုတွင်းထဲသို့ ပလပ်စတစ်ထိုးသွင်းသည့်အမြန်နှုန်းသည် စဉ်ဆက်မပြတ်အမြန်နှုန်းသို့ရောက်ရှိပြီး ပုံသွင်းထုတ်ကုန်များ၏ အသွင်အပြင်နှင့် အတွင်းပိုင်းအရည်အသွေးကို မြှင့်တင်ပေးပါသည်။
ထို့ကြောင့် ဆေးထိုးခြင်းလုပ်ငန်းစဉ်သည် အချိန်ထိန်းချုပ်မှုအစား အနေအထားထိန်းချုပ်မှုကို အသုံးပြုသည်။ဖိအားကို အချိန်အားဖြင့် ထိန်းချုပ်သည်။အချိန်ကြာကြာကိုင်ထားလျှင် ထုတ်ကုန်သိပ်သည်းဆ မြင့်သည်၊ အလေးချိန် လေးလံသည်၊ အတွင်းစိတ်ဖိစီးမှု ကြီးမားသည်၊ ပုံသွင်းရန် ခက်ခဲသည်၊ ဖြူစင်ရန် လွယ်ကူသည်၊ နှင့် ပုံသွင်းမှု လည်ပတ်မှုကို သက်တမ်းတိုးသည်။ကိုင်ဆောင်ချိန်က တိုလွန်းပါက၊ ထုတ်ကုန်သည် အစွန်းအထင်းများနှင့် မတည်ငြိမ်သောအတိုင်းအတာများ ဖြစ်နိုင်သည်။
အအေးခံချိန်-ထုတ်ကုန်၏ပုံသဏ္ဍာန်တည်ငြိမ်ကြောင်းသေချာစေရန်ဖြစ်သည်။ထုတ်ကုန်ထဲသို့ ပလပ်စတစ်မှိုအပေါက်ထဲသို့ ထိုးသွင်းပြီးနောက် လုံလောက်သော အအေးခံခြင်းနှင့် ပုံသွင်းချိန် လိုအပ်သည်။မဟုတ်ပါက၊ မှိုပွင့်သောအခါတွင် ထုတ်ကုန်သည် ကွဲထွက်လွယ်ပြီး ပုံပျက်လွယ်ကာ ထုတ်လွှတ်မှုသည် ပုံပျက်လွယ်ကာ အဖြူရောင်ဖြစ်လာသည်။အအေးခံချိန်သည် ရှည်လွန်းသဖြင့် ပုံသွင်းစက်ဝန်းကို ရှည်စေပြီး စီးပွားရေးအဆင်မပြေပါ။
အပိုင်းငါး- ရာထူးထိန်းချုပ်မှု
မှိုရွေ့လျားမှုအနေအထားသည် မှိုအဖွင့်မှိုပိတ်ခြင်းနှင့် လော့ခ်ချခြင်းအထိ ရွေ့လျားနေသည့်အကွာအဝေးတစ်ခုလုံးကို မှိုရွှေ့သည့်အနေအထားဟု ခေါ်သည်။မှိုကိုရွှေ့ရန် အကောင်းဆုံးအနေအထားမှာ ထုတ်ကုန်ကို ချောမွေ့စွာထုတ်နိုင်ခြင်းဖြစ်သည်။မှိုအဖွင့်အကွာအဝေးသည် ကြီးလွန်းပါက ပုံသွင်းစက်ဝိုင်းသည် ရှည်လိမ့်မည်။
မှိုပံ့ပိုးမှု အနေအထားကို ထိန်းချုပ်ထားသရွေ့ မှိုမှ ထုတ်လွှတ်သည့် အနေအထားကို အလွယ်တကူ ဖယ်ရှားနိုင်ပြီး ထုတ်ကုန်ကို ဖယ်ရှားနိုင်သည်။
သိုလှောင်မှုတည်နေရာ-ပထမဦးစွာ ပုံသွင်းထားသော ထုတ်ကုန်ထဲသို့ ထိုးသွင်းသည့် ပလတ်စတစ်ပမာဏကို သေချာစေရမည်ဖြစ်ပြီး ဒုတိယအချက်မှာ စည်အတွင်း သိမ်းဆည်းထားသော ပစ္စည်းပမာဏကို ထိန်းချုပ်ရမည်ဖြစ်သည်။သိုလှောင်မှုအနေအထားကို ရိုက်ချက်တစ်ခုထက်ပို၍ ထိန်းချုပ်ထားပါက၊ ထုတ်ကုန်သည် အလွယ်တကူ flash လိမ့်မည်၊ သို့မဟုတ်ပါက ထုတ်ကုန်သည် မလုံလောက်ဘဲ ဖြစ်ပေါ်လာလိမ့်မည်။
စည်တွင် ပစ္စည်း အလွန်အကျွံရှိနေပါက၊ ပလပ်စတစ်သည် စည်အတွင်း၌ အချိန်အတော်ကြာ ရှိနေမည်ဖြစ်ပြီး၊ ထုတ်ကုန်သည် အလွယ်တကူ အရောင်မှိန်သွားကာ ပုံသွင်းထားသော ထုတ်ကုန်၏ ခိုင်ခံ့မှုကို ထိခိုက်စေပါသည်။ဆန့်ကျင်ဘက်အနေနှင့်၊ ၎င်းသည် ပလတ်စတစ်ပလပ်စတစ်ပြုလုပ်ခြင်း၏ အရည်အသွေးကို ထိခိုက်စေပြီး ဖိအားထိန်းသိမ်းထားစဉ်အတွင်း မှိုထဲသို့ မည်သည့်ပစ္စည်းမျှ ဖြည့်သွင်းခြင်းမရှိသောကြောင့် ထုတ်ကုန်၏ ပုံသွင်းမှုမလုံလောက်ခြင်းနှင့် အစွန်းအထင်းများကို ဖြစ်ပေါ်စေပါသည်။
နိဂုံး
ဆေးထိုးပုံသွင်းထုတ်ကုန်များ၏ အရည်အသွေးတွင် ထုတ်ကုန်ဒီဇိုင်း၊ ပလပ်စတစ်ပစ္စည်းများ၊ မှိုဒီဇိုင်းနှင့် ပြုပြင်ထုတ်လုပ်သည့် အရည်အသွေး၊ ဆေးထိုးပုံသွင်းစက်ရွေးချယ်မှုနှင့် လုပ်ငန်းစဉ် ချိန်ညှိမှုတို့ ပါဝင်ပါသည်။ ဆေးထိုးခြင်းလုပ်ငန်းစဉ် ချိန်ညှိမှုသည် အချို့သောအချက်မှ စတင်၍မဖြစ်နိုင်သော်လည်း ဆေးထိုးခြင်းလုပ်ငန်းစဉ်၏ နိယာမမှ စတင်ရမည်ဖြစ်ပါသည်။ .ပြဿနာများကို ကျယ်ကျယ်ပြန့်ပြန့် ထည့်သွင်းစဉ်းစားခြင်း၊ ပြုပြင်ပြောင်းလဲမှုများကို ရှုထောင့်ပေါင်းစုံမှ တစ်ခုပြီးတစ်ခု ပြုလုပ်နိုင်သည် သို့မဟုတ် ပြဿနာများစွာကို တစ်ပြိုင်နက်တည်း ချိန်ညှိနိုင်သည်။သို့သော်လည်း ချိန်ညှိမှုနည်းလမ်းနှင့် နိယာမသည် ထိုအချိန်က ထုတ်လုပ်သည့် ထုတ်ကုန်များ၏ အရည်အသွေးနှင့် လုပ်ငန်းစဉ် အခြေအနေများပေါ်တွင် မူတည်ပါသည်။
ပို့စ်အချိန်- Nov-15-2023