The bearing seat is a structural part used to support the bearing and is a key transmission auxiliary part. It is used to fix the outer ring of the bearing and allow the inner ring to rotate continuously at high speed and high precision along the rotation axis.
Technical requirements for bearing seats
The accuracy of the bearing seat directly affects the accuracy of the transmission. The accuracy of the bearing seat is mainly concentrated in the bearing mounting hole, bearing positioning step and mounting support surface. Since the bearing is a standard purchased part, the bearing outer ring should be used as the benchmark when determining the fit of the bearing seat mounting hole and the bearing outer ring, that is, using When the transmission accuracy is high, the bearing mounting hole must have a higher circularity (cylindrical) requirement; the bearing positioning step must have a certain verticality requirement with the axis of the bearing mounting hole, and the installation support surface must also be consistent with the axis of the bearing mounting hole. Bearing mounting holes have certain parallelism and verticality requirements.
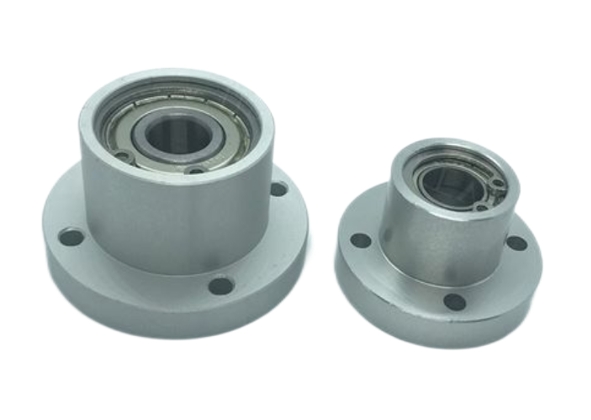
Process analysis of bearing seats
1) The main accuracy requirements of the bearing seat are the inner hole, bottom surface and the distance from the inner hole to the bottom surface. The inner hole is the most important surface of the bearing that plays a supporting or positioning role. It usually coincides with the moving shaft or bearing. The dimensional tolerance of the inner hole diameter is generally 17, and some precision bearing seat parts are TT6. The tolerance of the inner hole should generally be controlled within the aperture tolerance, and some precision parts should be controlled within the aperture tolerance of 13-12. For bearing seats, in addition to the requirements for cylindricity and coaxiality, attention should also be paid to the requirements for the straight line of the hole axis. In order to ensure the function of the part and improve its wear resistance, the surface roughness of the inner hole is generally Ral.6~3.2um.
2) If the machine tool uses two bearing seats at the same time, then the inner holes of the two bearing seats must be Ral.6~3.2um. Processing at the same time on the same machine tool can ensure that the distance from the center line of the two holes to the bottom surface of the bearing seat is equal.
Bearing seat materials and heat treatment
1) The materials of bearing seat parts are generally cast iron, steel and other materials.
2) Cast iron parts should be aged to remove the internal stress of casting and make its structural properties uniform.
GPM’s Machining Capabilities:
GPM has 20 years experience in CNC machining of different kinds of precision parts. We have worked with customers in many industries, including semiconductor, medical equipment, etc., and are committed to providing customers with high-quality, precise machining services. We adopt a strict quality management system to ensure that every part meets customer expectations and standards.
Post time: Jan-31-2024