In the precision parts manufacturing industry, aluminum alloy parts have attracted much attention due to their unique performance advantages and wide application prospects. CNC processing technology has become an important means of manufacturing aluminum alloy parts. This article will introduce in detail the basic concepts and performance advantages of aluminum alloys, as well as the challenges faced and corresponding solutions during CNC machining. By understanding these contents, we will be able to better grasp the key points of manufacturing aluminum alloy parts and produce equipment parts that meet different application scenarios.
Content
Part One: What is aluminum alloy?
Part Two: What are the performance advantages of aluminum alloy processing?
Part Three: What are the difficulties when CNC processing aluminum alloy parts and how to avoid them?
Part One: What is aluminum alloy?
Aluminum alloy is a metal material whose main component is aluminum but also contains small amounts of other metal elements. According to the added elements and proportions, aluminum alloys can be divided into different types, such as: #1, #2,#3, #4, #5 , #6 , #7 , #8 and #9 series. The #2 series aluminum alloy is mainly characterized by high hardness but poor corrosion resistance, with copper as the main component. Representative ones include 2024, 2A16, 2A02, etc. This type of alloy is often used to make aerospace parts. The 3 series aluminum alloy is an aluminum alloy with manganese as the main alloy element. It has good corrosion resistance and welding performance, and can improve its strength through cold work hardening. In addition, there are #4 series aluminum alloys, usually with silicon content between 4.5-6.0% and high strength. Representative ones include 4A01 and so on.
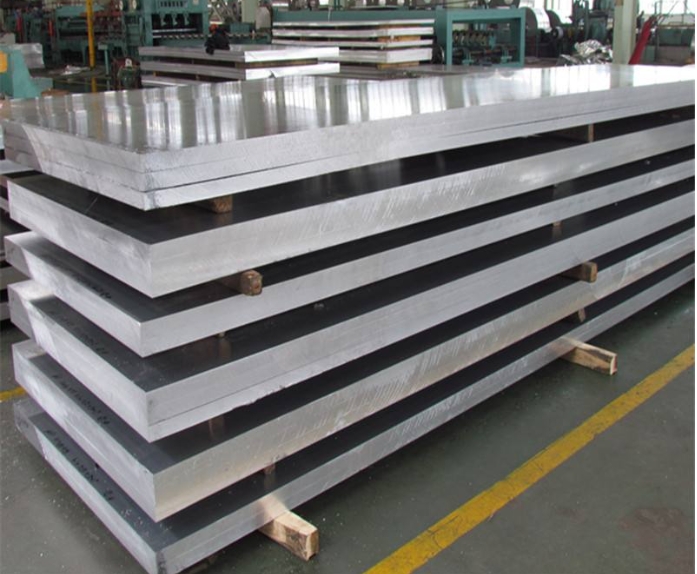
Part Two: What are the performance advantages of aluminum alloy processing?
Aluminum alloys also excel in terms of machinability. Aluminum alloy has low density, light weight, and high strength, about 1/3 lighter than ordinary steel. About 1/2 lighter than stainless steel. Secondly, aluminum alloy is easy to process, form and weld, can be made into various shapes, and is suitable for various processing techniques, such as milling, drilling, cutting, drawing, deep drawing, etc. In addition, it costs less than steel and requires less power to process, saving processing costs.
In addition, aluminum is a negatively charged metal that can form a protective oxide film on the surface under natural conditions or through anodization, and its corrosion resistance is much better than steel.
The main types of aluminum alloys commonly used in CNC processing are aluminum 6061 and aluminum 7075. Aluminum 6061 is the most commonly used material for CNC machining. It has good corrosion resistance, weldability, moderate strength, and good oxidation effect, so it is often used in auto parts, bicycle frames, sporting goods and other fields. Aluminum 7075 is one of the strongest aluminum alloys. The material has high strength, is easy to process, has good wear resistance, corrosion resistance and oxidation resistance. Therefore, it is often selected as a material for high-strength entertainment equipment, automobiles and aerospace frames.

Part Three: What are the difficulties when CNC processing aluminum alloy parts and how to avoid them?
First of all, because the hardness of aluminum alloy is relatively soft, it is easy to stick to the tool, which may cause the surface finish of the workpiece to be unqualified. You can consider changing the processing parameters during processing, such as avoiding medium-speed cutting, because this can easily lead to tool sticking. Secondly, the melting point of aluminum alloy is low, so tooth breakage is prone to occur during the cutting process. Therefore, using cutting fluid with good lubrication and cooling properties can effectively solve the problems of tool sticking and tooth breakage. In addition, cleaning after aluminum alloy processing is also a challenge, because if the cleaning ability of the aluminum alloy cutting fluid is not good, there will be residues on the surface, which will affect the appearance or subsequent printing processing. To avoid mildew problems caused by cutting fluid, the corrosion inhibition ability of the cutting fluid should be improved and the storage method after processing should be improved.
GPM’s CNC machining services for aluminum alloy parts:
GPM is a manufacturer that has focused on CNC processing of precision parts for 20 years.When manufacturing aluminum parts, GPM will review each project based on part complexity and manufacturability, evaluate production costs, and select a process route that meets your design and specifications. We use 3-, 4-, and 5-axis CNC milling. , CNC turning combined with other manufacturing processes can easily handle various machining challenges while helping you save time and costs.
Post time: Nov-01-2023