In the molding process of converting plastic particles into plastic products, plastics are often subjected to high temperature and high pressure, and flow molding at high shear rates. Different molding conditions and processes will have different effects on product quality. Injection molding has plastic It consists of four aspects: raw materials, injection molding machine, mold and injection molding process.
The quality of products includes internal material quality and appearance quality. Internal material quality is mainly mechanical strength, and the size of internal stress directly affects the mechanical strength of the product. The main reasons for generating internal stress are determined by the crystallinity of the product and the orientation of molecules in plastic molding. of. The appearance quality of the product is the surface quality of the product, but warping and deformation of the product caused by large internal stress will also affect the appearance quality. The appearance quality of products includes: insufficient products, product dents, weld marks, flash, bubbles, silver wires, black spots, deformation, cracks, delamination, peeling and discoloration, etc., all related to molding temperature, pressure, flow, time and position. related.
Content
Part One: Molding temperature
Part Two: Molding process pressure
Part three: Injection molding machine speed
Part Four: Time setting
Part Five: Position Control
Part One: Molding temperature
Barrel temperature: It is the melting temperature of the plastic. If the barrel temperature is set too high, the viscosity of the plastic after melting is low. Under the same injection pressure and flow rate, the injection speed is fast, and the molded products are prone to flash, silver, discoloration and brittleness.
The temperature of the barrel is too low, the plastic is poorly plasticized, the viscosity is high, the injection speed is slow under the same injection pressure and flow rate, the molded products are easily insufficient, the weld marks are obvious, the dimensions are unstable and there are cold blocks in the products.
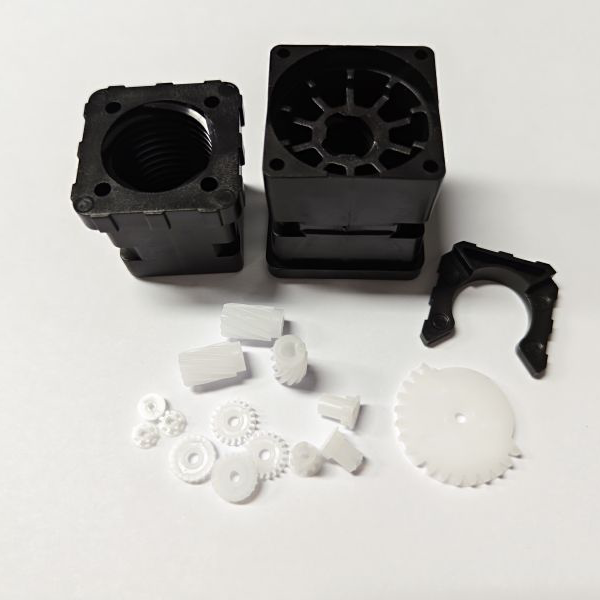
Nozzle temperature: If the nozzle temperature is set high, the nozzle will easily drool, causing cold filaments in the product. Low nozzle temperature causes clogging of the mold pouring system. The injection pressure must be increased to inject plastic, but there will be cold material in the molded product immediately.
Mold temperature: If the mold temperature is high, the injection pressure and flow rate can be set lower. However, at the same pressure and flow rate, the product will easily flash, warp and deform, and it will be difficult to eject the product from the mold. The mold temperature is low, and under the same injection pressure and flow rate, the product is insufficiently formed, with bubbles and weld marks, etc.
Plastic drying temperature: Various plastics have different drying temperatures. ABS plastics generally set a drying temperature of 80 to 90°C, otherwise it will be difficult to dry and evaporate the moisture and residual solvents, and the products will easily have silver wires and bubbles, and the strength of the products will also decrease.
Part Two: Molding process pressure
Pre-molding back pressure: high back pressure and high storage density means more material can be stored within the same storage volume. Low back pressure means low storage density and less storage material. After setting the storage position, and then making a large adjustment to the back pressure, you must pay attention to resetting the storage position, otherwise it will easily cause flash or insufficient product.
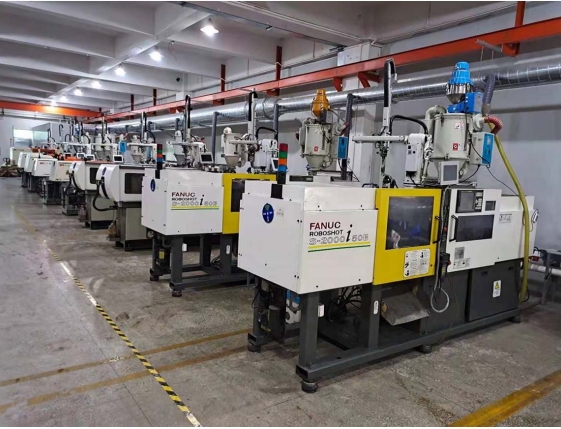
Injection pressure: Different types of plastics have different melt viscosities. The viscosity of amorphous plastics changes greatly with changes in plasticizing temperature. The injection pressure is set according to the welding viscosity of the plastic and the plastic process ratio. If the injection pressure is set too low, the product will be insufficiently injected, resulting in dents, weld marks and unstable dimensions. If the injection pressure is too high, the product will have flash, discoloration and difficulty in mold ejection.
Clamping pressure: It depends on the projected area of the mold cavity and the injection pressure. If the clamping pressure is insufficient, the product will easily flash and increase in weight. If the clamping force is too large, it will be difficult to open the mold. Generally, the clamping pressure setting should not exceed 120par/cm2.
Holding pressure: When the injection is completed, the screw continues to be given a pressure called holding pressure. At this time, the product in the mold cavity has not yet frozen. Maintaining pressure can continue to fill the mold cavity to ensure that the product is full. If the holding pressure and pressure setting are too high, it will bring great resistance to the support mold and the pull-out core. The product will easily turn white and warp. In addition, the mold runner gate will be easily expanded and tightened by the supplementary plastic, and the gate will be broken in the runner. If the pressure is too low, the product will have dents and unstable dimensions.
The principle of setting the ejector and neutron pressure is to set the pressure based on the overall size of the mold cavity area, the core projection area of the inserted core, and the geometric complexity of the molded product. size. Generally, this requires setting the pressure of the supporting mold and the neutron cylinder to be able to push the product.
Part three: Injection molding machine speed
Screw speed: In addition to adjusting the pre-plastic flow rate, it is mainly affected by the pre-plastic back pressure. If the pre-molding flow rate is adjusted to a large value and the pre-molding back pressure is high, as the screw rotates, the plastic will have a large shear force in the barrel, and the plastic molecular structure will be easily cut off. The product will have black spots and black stripes, which will affect the appearance quality and strength of the product. , and the barrel heating temperature is difficult to control. If the pre-plastic flow rate is set too low, the pre-plastic storage time will be extended, which will affect the molding cycle.
Injection speed: The injection speed must be set reasonably, otherwise it will affect product quality. If the injection speed is too fast, the product will have bubbles, burnt, discolored, etc. If the injection speed is too slow, the product will be insufficiently formed and have weld marks.
Support mold and neutron flow rate: should not be set too high, otherwise the ejection and core pulling movements will be too fast, resulting in unstable ejection and core pulling, and the product will easily turn white.
Part Four: Time setting
Drying time: It is the drying time for plastic raw materials. Various types of plastics have optimal drying temperatures and times. The drying temperature of ABS plastic is 80~90℃ and the drying time is 2 hours. ABS plastic generally absorbs 0.2 to 0.4% water within 24 hours, and the water content that can be injection molded is 0.1 to 0.2%.
Injection and pressure holding time: The control method of the computer injection machine is equipped with multi-stage injection to adjust the pressure, speed and injection plastic amount in stages. The speed of plastic injected into the mold cavity reaches a constant speed, and the appearance and internal material quality of the molded products are improved.
Therefore, the injection process usually uses position control instead of time control. The holding pressure is controlled by time. If the holding time is long, the product density is high, the weight is heavy, the internal stress is large, demoulding is difficult, easy to whiten, and the molding cycle is extended. If the holding time is too short, the product will be prone to dents and unstable dimensions.
Cooling time: It is to ensure that the product is stable in shape. It requires sufficient cooling and shaping time after the plastic injected into the mold cavity is molded into the product. Otherwise, the product is easy to warp and deform when the mold is opened, and the ejection is easy to deform and become white. The cooling time is too long, which prolongs the molding cycle and is uneconomical.
Part Five: Position Control
The mold shifting position is the entire moving distance from mold opening to mold closing and locking, which is called the mold shifting position. The best position to move the mold is to be able to take out the product smoothly. If the mold opening distance is too large, the molding cycle will be long.
As long as the position of the mold support is controlled, the position of ejection from the mold can be easily removed and the product can be removed.
Storage location: Firstly, the amount of plastic injected into the molded product must be ensured, and secondly, the amount of material stored in the barrel must be controlled. If the storage position is controlled by more than one shot, the product will easily flash, otherwise the product will be insufficiently formed.
If there is too much material in the barrel, the plastic will stay in the barrel for a long time, and the product will easily fade and affect the strength of the molded product. On the contrary, it affects the quality of plastic plasticization, and no material is replenished into the mold during pressure maintaining, resulting in insufficient molding of the product and dents.
Conclusion
The quality of injection molded products involves product design, plastic materials, mold design and processing quality, injection molding machine selection and process adjustment, etc. Injection process adjustment cannot only start from a certain point, but must start from the principle of the injection process. Comprehensive and comprehensive consideration of issues, adjustments can be made one by one from multiple aspects or multiple issues can be adjusted at once. However, the adjustment method and principle depend on the quality and process conditions of the products produced at that time.
Post time: Nov-15-2023