In today's manufacturing world, CNC machining technology has become an integral part of the manufacturing process due to its high precision and repeatability. However, to fully utilize the benefits of CNC technology, ensuring product quality is critical. Quality control plays a central role in CNC manufacturing, directly affecting production efficiency, costs, and the performance and reliability of the final product. This article will explore how to achieve effective quality control in the CNC manufacturing process.
Part 1: The Basic Concepts of Quality Control in CNC Machining
Quality control, as a series of systematic processes and measures to ensure that products meet the necessary quality standards, covers the entire production chain from raw material selection to final product delivery. This concept is particularly important in the CNC manufacturing environment, because any small error can lead to a lot of waste and product defects. Therefore, the goal of quality control is not only to maximize product qualification rate, but also to reduce costs by reducing scrap and rework, while improving customer satisfaction and market competitiveness.
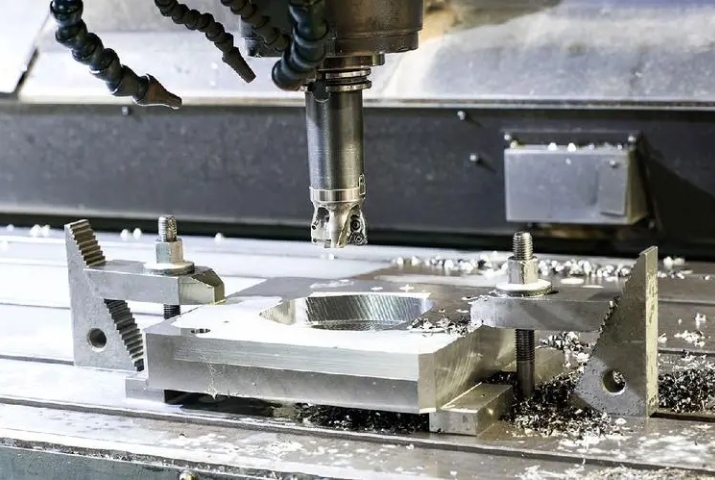
Part II: Key Strategies and Techniques of Quality Control in CNC Machining
1. Equipment and tool selection and maintenance
Choosing CNC machines and tools that are suitable for specific manufacturing needs is crucial to ensuring quality. High-quality equipment can perform cutting and forming tasks more accurately with fewer failures. In addition, regular maintenance and calibration are key to ensuring the long-term stability and accuracy of the equipment. Choosing the right machines and tools can not only improve processing efficiency, but also extend the life of the equipment and reduce long-term operating costs.
2. Operator training and management
Highly skilled operators are essential to achieve quality control. Investing in systematic training and continuous education of employees can significantly improve operational accuracy and efficiency and reduce error rates. Through regular training and assessment, employees are kept abreast of the latest CNC technology and ensure their operations meet the highest industry standards
3. Program Verification and Simulation
Before officially starting production, program verification and simulation can avoid potential errors. Using advanced CAD/CAM software can help detect possible flaws in the design and correct them before production. This not only improves production efficiency, but also ensures product consistency and quality.
4. Material selection and management
Choosing the right materials and ensuring their quality is the basis for ensuring the quality of the final product. At the same time, a reasonable material management and tracking system can ensure that each batch of materials used meets the standards. The consistency and quality of the materials directly affect the performance of the final product, so a strict material selection and management system is essential.
5. Environmental Control
The environmental conditions in which the CNC machine is located, such as temperature and humidity, will affect its processing accuracy. Therefore, maintaining a stable production environment is very critical to ensure product quality. By controlling these variables, quality problems caused by environmental factors can be reduced.
6. Improve the quality system
Strengthen the quality assurance measures in the production process, improve the stability of process quality, and ensure the effective implementation of quality functions in all links of the production process. Promote the quality supervision system and implement the reward and punishment mechanism to ensure that each link meets the quality standards and encourage employees to pay attention to and improve product quality.
7. Three-coordinate measurement
Through three-coordinate measurement, it is possible to accurately determine whether the error of the workpiece is within the allowable tolerance range, thereby avoiding product failure due to excessive errors. Based on the precise data provided by three-coordinate measurement, production personnel can adjust the processing technology, optimize production parameters, and reduce deviations in production. At the same time, a three-coordinate measuring machine can replace a variety of traditional surface measurement tools and expensive combination gauges, simplify measurement equipment, and improve measurement efficiency.
GPM was founded in 2004 and is a professional manufacturer of precision machinery parts. The company has invested a lot of money to introduce high-end imported hardware equipment. Through careful design and maintenance, professional operator training, precise program verification, real-time production monitoring and excellent materials, it effectively guarantees quality control in the manufacturing process. The company has ISO9001, ISO13485, ISO14001 and other system certifications and German Zeiss three-coordinate inspection equipment, ensuring that the company strictly abides by international standards in the production and management process.
Post time: Jun-29-2024