Części tarczowe są jednymi z typowych części powszechnie spotykanych podczas obróbki.Do głównych typów części tarcz zaliczają się: różne łożyska podtrzymujące wał napędowy, kołnierze, tarcze łożyskowe, płyty dociskowe, pokrywy końcowe, przezroczyste osłony kołnierzy itp. Każda z nich ma swój własny, niepowtarzalny kształt i funkcję.Jakość tych części ma bezpośredni wpływ na wydajność pracy i bezpieczeństwo sprzętu.Dlatego istnieją rygorystyczne wymagania dotyczące procesu produkcyjnego i kontroli jakości części tarczowych.
Zawartość
Część 1: Analiza technologii obróbki części tarczowych
Część 2: Kontrola dokładności przetwarzania części dyskowych
Część 3: Dobór materiałów na części tarczowe
Część 4: Obróbka cieplna części tarczowych
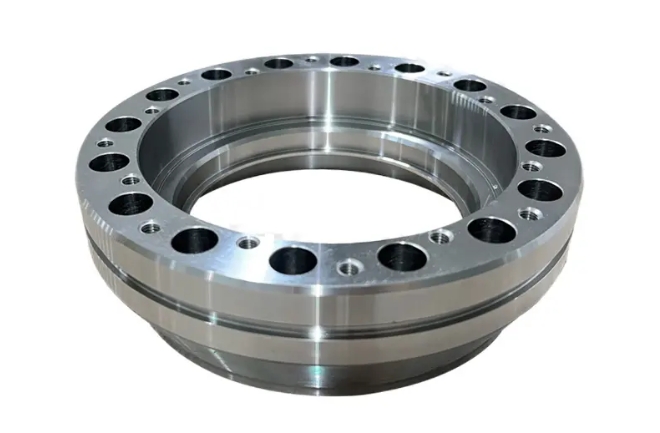
Część 1: Analiza technologii obróbki części tarczowych
Głównymi procesami obróbki części tarczowych są głównie obróbka zgrubna i wykańczająca otworu wewnętrznego i powierzchni zewnętrznej, szczególnie najważniejsza jest obróbka zgrubna i wykańczająca otworu.Powszechnie stosowane metody przetwarzania obejmują wiercenie, rozwiercanie, porównywanie otworów, szlifowanie otworów, wyciąganie otworów, szlifowanie otworów itp. Wśród nich wiercenie, rozwiercanie i otwory w osłonach są powszechnie stosowane jako obróbka zgrubna i półwykańczająca otworów.Dziurki od klucza, otwory szlifierskie itp. Otwory, otwory ciągnione i szlifowane stanowią wykończenie otworów.Przy ustalaniu planu obróbki otworu ogólnie stosuje się następujące zasady.
1) W przypadku otworów o mniejszych średnicach najczęściej przyjmuje się rozwiązanie wiercenia, rozpierania i wiercenia.
2) W przypadku otworów o większych średnicach większość z nich przyjmuje rozwiązanie wiercenia i dalszej obróbki wykańczającej.
3) W przypadku części ze stali hartowanej lub tulei o wyższych wymaganiach dotyczących precyzji należy zastosować rozwiązanie do szlifowania otworów.
Części tarczowe to stosunkowo złożone części konstrukcyjne składające się z wielu powierzchni czołowych, głębokich otworów, zakrzywionych powierzchni i konturów zewnętrznych.Dlatego pełnią głównie rolę wspierającą i łączącą w urządzeniach mechanicznych.W zależności od specyfiki i wymagań części należy dobrać odpowiednie metody przetwarzania i parametry procesu, a jednocześnie przeprowadzić ścisłą kontrolę jakości podczas przetwarzania.Na przykład w przypadku cienkościennych części tarczowych, ze względu na słabą sztywność, niewłaściwy dobór pozycji mocowania, siły mocowania i schematu mocowania podczas obróbki może łatwo spowodować odkształcenie mocowania, poważnie wpływając na dokładność obróbki części.Dlatego optymalizacja układu mocowania i parametrów siły mocowania jest kluczowym krokiem w celu ograniczenia odkształceń mocowania.
Część 2: Kontrola dokładności przetwarzania części dyskowych
Precyzyjne sterowanie jest również ważną częścią obróbki części dyskowych.Obejmuje to kontrolę dokładności wymiarowej, dokładności kształtu i dokładności pozycjonowania.Na przykład w przypadku niektórych części tarczy wymagających dużej precyzji, takich jak dokładność wymiarowa otworu wewnętrznego IT6, wymagana cylindryczność niektórych otworów i okręgów zewnętrznych wynosi ≤0,02 mm, wymagana płaskość dużej i małej powierzchni czołowej wynosi ≤0,02 mm, a wymagania dotyczące otworu Wymóg pionowości wynosi ≤0,02 mm.Wymaga to użycia precyzyjnego sprzętu i narzędzi podczas procesu obróbki, przy jednoczesnym zapewnieniu dużej precyzji głębokości.
Część 3: Dobór materiałów na części tarczowe
Części tarcz są często wykonane ze stali, żeliwa, brązu lub mosiądzu.Tarcze z małymi otworami zazwyczaj wybierają pręty walcowane na gorąco lub ciągnione na zimno.W zależności od materiału można wybrać odlewy pełne;gdy średnica otworu jest większa, można wykonać otwory wstępne.Jeśli partia produkcyjna jest duża, można wybrać zaawansowane procesy produkcyjne półproduktów, takie jak wytłaczanie na zimno, aby poprawić produktywność i zaoszczędzić materiały.
Część 4: Obróbka cieplna części tarczowych
1) Procesy obróbki cieplnej części tarcz obejmują normalizowanie, wyżarzanie, hartowanie i odpuszczanie, nawęglanie i hartowanie, hartowanie indukcyjne o wysokiej częstotliwości, azotowanie, starzenie, gotowanie i charakterystykę oleju itp.
2) Powszechnie stosowane urządzenia do obróbki cieplnej obejmują piece skrzynkowe, piece wielofunkcyjne, obrabiarki do hartowania indukcyjnego wysokiej częstotliwości, piece do nawęglania, piece do azotowania, piec do odpuszczania
Możliwości obróbki GPM:
GPM ma 20-letnie doświadczenie w obróbce CNC różnego rodzaju części precyzyjnych.Współpracowaliśmy z klientami z wielu branż, w tym półprzewodników, sprzętu medycznego itp., i jesteśmy zaangażowani w zapewnianie klientom wysokiej jakości usług precyzyjnej obróbki.Stosujemy rygorystyczny system zarządzania jakością, aby zapewnić, że każda część spełnia oczekiwania i standardy klientów.
Informacja o prawach autorskich:
GPM Intelligent Technology(Guangdong) Co., Ltd. advocates respect and protection of intellectual property rights and indicates the source of articles with clear sources. If you find that there are copyright or other problems in the content of this website, please contact us to deal with it. Contact information: marketing01@gpmcn.com
Czas publikacji: 16 stycznia 2024 r