యంత్రాల తయారీ రంగంలో, బాక్స్ భాగాలు ఒక సాధారణ రకం నిర్మాణ భాగాలు మరియు వివిధ యాంత్రిక పరికరాలలో విస్తృతంగా ఉపయోగించబడతాయి.దాని సంక్లిష్ట నిర్మాణం మరియు అధిక ఖచ్చితత్వ అవసరాల కారణంగా, బాక్స్ భాగాల ప్రాసెసింగ్ సాంకేతికత ముఖ్యంగా క్లిష్టమైనది.ఈ కథనం పాఠకులకు సంబంధిత జ్ఞానాన్ని బాగా అర్థం చేసుకోవడానికి మరియు నైపుణ్యం పొందడంలో సహాయపడటానికి బాక్స్ భాగాల ప్రాసెసింగ్ సాంకేతికతను సమగ్రంగా మరియు వృత్తిపరంగా వివరిస్తుంది.
విషయము:
పార్ట్ 1. బాక్స్ భాగాల నిర్మాణ లక్షణాలు
పార్ట్ 2. బాక్స్ భాగాల కోసం ప్రాసెసింగ్ అవసరాలు
పార్ట్ 3. బాక్స్ భాగాల ప్రెసిషన్ మ్యాచింగ్
పార్ట్ 4. బాక్స్ భాగాల తనిఖీ
1. బాక్స్ భాగాల నిర్మాణ లక్షణాలు
సంక్లిష్ట రేఖాగణిత ఆకారాలు
పెట్టె భాగాలు సాధారణంగా బహుళ ఉపరితలాలు, రంధ్రాలు, స్లాట్లు మరియు ఇతర నిర్మాణాలతో కూడి ఉంటాయి మరియు లోపలి భాగం కుహరం ఆకారంలో, సన్నని మరియు అసమాన గోడలతో ఉండవచ్చు.ఈ సంక్లిష్ట నిర్మాణానికి పెట్టె భాగాల రూపకల్పన మరియు తయారీ ప్రక్రియలో అనేక అంశాల ఖచ్చితమైన నియంత్రణ అవసరం.
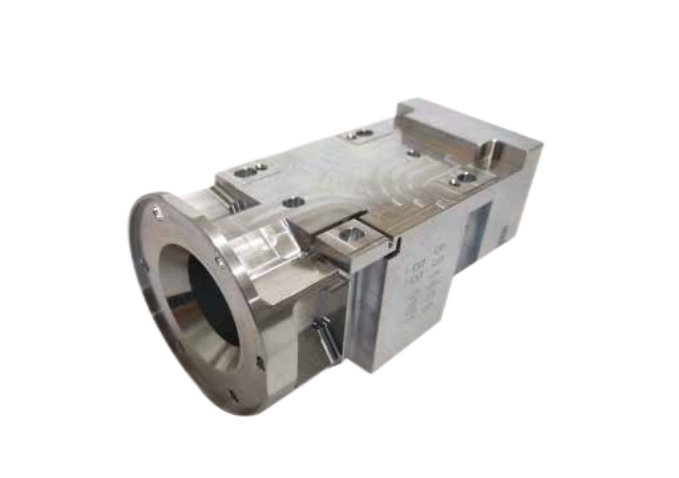
అధిక ఖచ్చితత్వ అవసరాలు
బాక్స్ భాగాల ప్రాసెసింగ్ డిజైన్ అవసరాలను తీర్చడానికి ప్రతి ఉపరితలం యొక్క సమాంతరత మరియు లంబంగా మాత్రమే అవసరం, కానీ రంధ్రాల స్థాన ఖచ్చితత్వాన్ని కూడా కలిగి ఉంటుంది.బాక్స్ భాగాల సాధారణ ఆపరేషన్ను నిర్ధారించడానికి ఇవి కీలకమైన అంశాలు.
మెటీరియల్ లక్షణాలు
పెట్టె భాగాలకు సాధారణంగా ఉపయోగించే పదార్థాలు కాస్ట్ ఇనుము లేదా తారాగణం ఉక్కు.ఈ పదార్థాల కట్టింగ్ పనితీరు సాపేక్షంగా పేలవంగా ఉంది, ఇది ప్రాసెసింగ్ కష్టాన్ని పెంచుతుంది.
2. బాక్స్ భాగాల కోసం ప్రాసెసింగ్ అవసరాలు
డైమెన్షనల్ మరియు ఆకార ఖచ్చితత్వాన్ని నిర్ధారించుకోండి
బాక్స్ భాగాల ప్రాసెసింగ్ సమయంలో, అసెంబ్లీ మరియు ఉపయోగం యొక్క అవసరాలకు అనుగుణంగా పరిమాణం మరియు ఆకృతి యొక్క ఖచ్చితత్వం ఖచ్చితంగా నియంత్రించబడాలి.
స్థానం ఖచ్చితత్వం
రంధ్రాల స్థానాల ఖచ్చితత్వం పెట్టె భాగాలకు చాలా ముఖ్యమైనది, ఎందుకంటే రంధ్రం స్థానాల యొక్క ఖచ్చితత్వం మొత్తం యాంత్రిక వ్యవస్థ యొక్క ఆపరేషన్ ఖచ్చితత్వం మరియు స్థిరత్వానికి నేరుగా సంబంధించినది.
ఉపరితల కరుకుదనం
పెట్టె భాగాల యొక్క సంపర్క దృఢత్వం మరియు పరస్పర స్థాన ఖచ్చితత్వాన్ని నిర్ధారించడానికి, ప్రధాన విమానాల ఆకృతి ఖచ్చితత్వం మరియు ఉపరితల కరుకుదనం అధిక ప్రమాణాలను చేరుకోవాలి.
ఫాలో-అప్ ప్రాసెసింగ్
మ్యాచింగ్తో పాటు, బాక్స్ భాగాలు కూడా వాటి ప్రదర్శన నాణ్యత మరియు మన్నికను మెరుగుపరచడానికి శుభ్రపరచడం, తుప్పు పట్టడం మరియు పెయింటింగ్ వంటి ప్రాసెసింగ్ పూర్తయిన తర్వాత తదుపరి చికిత్సల శ్రేణిని కూడా చేయించుకోవాలి.
బాక్స్ భాగాల ఖచ్చితమైన మ్యాచింగ్
బాక్స్ భాగాలను పూర్తి చేయడం అనేది చాలా ఎక్కువ ఖచ్చితత్వం అవసరమయ్యే ప్రక్రియ, ఇది మొత్తం మెకానికల్ సిస్టమ్ యొక్క అసెంబ్లీ నాణ్యత మరియు పనితీరుకు నేరుగా సంబంధించినది.పెట్టె భాగాలను పూర్తి చేసేటప్పుడు, ఈ క్రింది సమస్యలకు ప్రత్యేక శ్రద్ధ అవసరం:
యంత్రం మరియు సాధనం ఎంపిక
హై-ప్రెసిషన్ ప్రాసెసింగ్ ఫలితాలను సాధించడానికి, హై-ప్రెసిషన్ మెషిన్ టూల్స్ మరియు కట్టింగ్ టూల్స్ తప్పనిసరిగా ఉపయోగించాలి.ఇందులో CNC వర్టికల్ లాత్లు, CNC వర్టికల్ మ్యాచింగ్ సెంటర్లు మరియు క్షితిజసమాంతర మ్యాచింగ్ సెంటర్లు, అలాగే బాక్స్ ఫినిషింగ్కు అంకితమైన హై-ప్రెసిషన్ టూల్స్ వంటి అధిక-సామర్థ్య పరికరాలు ఉన్నాయి, కానీ వీటికే పరిమితం కాదు.
ప్రాసెసింగ్ పారామితుల ఆప్టిమైజేషన్
పూర్తి చేసే ప్రక్రియలో, కట్టింగ్ స్పీడ్ మరియు ఫీడ్ రేట్ వంటి పారామితులను ఖచ్చితంగా నియంత్రించాలి.చాలా ఎక్కువ లేదా చాలా తక్కువగా ఉన్న పారామీటర్ సెట్టింగ్లు ప్రాసెసింగ్ నాణ్యతను ప్రభావితం చేయవచ్చు, ఉదాహరణకు భాగం వైకల్యానికి కారణమయ్యే అధిక కట్టింగ్ శక్తులను ఉత్పత్తి చేయడం లేదా ప్రాసెసింగ్ సామర్థ్యం చాలా తక్కువగా ఉంటుంది.
ఉష్ణోగ్రత మరియు రూపాంతరం నియంత్రణ
పూర్తి చేసే ప్రక్రియలో, సుదీర్ఘ నిరంతర కట్టింగ్ సమయం కారణంగా, వేడెక్కడం సులభం, దీని ఫలితంగా సరికాని భాగం కొలతలు లేదా ఉపరితల నాణ్యత తగ్గుతుంది.అందువల్ల, శీతలకరణిని ఉపయోగించడం, ప్రాసెసింగ్ క్రమాన్ని సహేతుకంగా ఏర్పాటు చేయడం మరియు ఉష్ణోగ్రతను నియంత్రించడానికి మరియు ఉష్ణ వైకల్యాన్ని తగ్గించడానికి విశ్రాంతి సమయం వంటి చర్యలు తీసుకోవాలి.
రంధ్రం మ్యాచింగ్ ఖచ్చితత్వం
పెట్టె భాగాలలో హోల్ ప్రాసెసింగ్ అనేది ప్రత్యేక శ్రద్ధ అవసరం, ప్రత్యేకించి చాలా ఎక్కువ స్థాన ఖచ్చితత్వం మరియు ఏకాక్షకత్వం అవసరమయ్యే రంధ్రాల కోసం.రంధ్రాల యొక్క డైమెన్షనల్ ఖచ్చితత్వం మరియు ఉపరితల నాణ్యతను నిర్ధారించడానికి బోరింగ్, రీమింగ్, రీమింగ్ మరియు ఇతర పద్ధతులను ఉపయోగించాలి.అదే సమయంలో, విచలనాలను నివారించడానికి రంధ్రాల మధ్య స్థాన సంబంధానికి శ్రద్ధ ఉండాలి.
వర్క్పీస్ బిగింపు పద్ధతి
ప్రాసెసింగ్ ఖచ్చితత్వాన్ని నిర్ధారించడానికి సరైన బిగింపు పద్ధతి కీలకం.ప్రాసెసింగ్ సమయంలో వర్క్పీస్ యొక్క స్థిరత్వాన్ని నిర్ధారించడానికి మరియు సరికాని బిగింపు వల్ల కలిగే ప్రాసెసింగ్ లోపాలను నివారించడానికి తగిన సాధనాన్ని రూపొందించాలి.ఉదాహరణకు, పరివర్తన థ్రెడ్ రంధ్రాల పద్ధతిని ఉపయోగించి ఒక బిగింపులో పెద్ద ఉపరితలాల మిల్లింగ్ మరియు డ్రిల్లింగ్ను పూర్తి చేయవచ్చు, ఫ్లాట్నెస్ను సమర్థవంతంగా మెరుగుపరుస్తుంది.
4. బాక్స్ భాగాల తనిఖీ
మెకానికల్ సిస్టమ్ యొక్క ఖచ్చితత్వం మరియు పనితీరు అవసరాలకు అనుగుణంగా ఉండేలా బాక్స్ భాగాల తనిఖీ ఒక కీలక దశ.తనిఖీ ప్రక్రియలో, అనేక వివరాలకు శ్రద్ద అవసరం.
కొలిచే సాధనాలు
అధిక-ఖచ్చితమైన కొలత ఫలితాలను సాధించడానికి, త్రీ-డైమెన్షనల్ కోఆర్డినేట్ కొలిచే యంత్రాలు వంటి అధిక-స్థిరత్వం మరియు అధిక-సామర్థ్య కొలత సాధనాలను ఉపయోగించడం అవసరం.ఈ పరికరాలు బాక్స్ భాగాల కొలతలు, ఫ్లాట్నెస్, కోక్సియాలిటీ మొదలైన వాటి యొక్క ఖచ్చితమైన కొలతల శ్రేణిని సాధించగలవు.
కొలత ఉపకరణాలను కాన్ఫిగర్ చేయండి
లోతైన రంధ్రాలు మరియు కావిటీలలో కొలతలు కొలత ఖచ్చితత్వాన్ని నిర్ధారించడానికి టెస్ట్ బేస్ ఎక్స్టెన్షన్ రాడ్లు, స్టార్-ఆకారపు స్టైలీ మొదలైన వాటికి తగిన పొడిగింపు రాడ్లు మరియు స్టైలీ అవసరం.
స్థానాలను నిర్ణయించండి
కొలిచే ముందు, బాక్స్ భాగాల స్థాన పద్ధతిని స్పష్టం చేయడం అవసరం.పొజిషనింగ్ కోసం మూడు పరస్పర లంబ ఉపరితలాలు లేదా పొజిషనింగ్ కోసం రెండు లంబ రంధ్రాలతో కూడిన విమానం సాధారణంగా ఉపయోగించబడతాయి.ఇది కొలత యొక్క పునరావృత మరియు స్థిరత్వాన్ని మెరుగుపరచడానికి సహాయపడుతుంది.
మౌంటు పద్ధతులను పరిగణించండి
పెట్టె భాగాలు సాపేక్షంగా పెద్ద పరిమాణంలో మరియు బరువులో భారీగా ఉన్నాయని పరిగణనలోకి తీసుకుంటే, బిగించేటప్పుడు సౌలభ్యం, పునరావృతం మరియు స్థిరత్వం ఉండేలా చూసుకోవాలి.వారు కొలత కోసం పని ఉపరితలంపై నేరుగా ఉంచవచ్చు లేదా సార్వత్రిక బిగింపులు లేదా సాధారణ బిగింపులను ఉపయోగించి వాటిని పరిష్కరించవచ్చు.
జాగ్రత్తలు పాటించండి
కొలిచేటప్పుడు, మీరు భాగాలు శుభ్రంగా మరియు బర్ర్స్ లేకుండా తుడిచిపెట్టినట్లు నిర్ధారించుకోవాలి, కొలత మూలకాల యొక్క ఉపరితల ఖచ్చితత్వాన్ని ఎక్కువగా ఉంచండి మరియు భాగాల యొక్క పొరపాటు కదలికను నివారించడానికి తగిన కొలత వేగాన్ని ఎంచుకోండి, ప్రత్యేకించి అనేక పరిమాణాలు ఉన్నప్పుడు.అదే సమయంలో, నేరుగా కొలవడం కష్టంగా ఉన్న స్థానాల కోసం, బహుళ బిగింపు లేదా పరోక్ష కొలత పద్ధతులను పరిగణించవచ్చు.
కొలత డేటాను విశ్లేషించండి
కొలిచిన డేటాను జాగ్రత్తగా విశ్లేషించాల్సిన అవసరం ఉంది, ప్రత్యేకించి హోల్ డైమెన్షనల్ ఖచ్చితత్వం, స్థూపాకారత మరియు ఏకాక్షకత వంటి కీలక పారామితులు, కొలత ఫలితాల యొక్క ఖచ్చితత్వం మరియు విశ్వసనీయతను నిర్ధారించడానికి ప్రాసెసింగ్ మరియు అసెంబ్లీ యొక్క వాస్తవ పరిస్థితులతో కలిపి విశ్లేషించాలి.
కొలత నైపుణ్యాలను నిర్ధారించండి
రంధ్ర అక్షాన్ని కొలిచేటప్పుడు, మీరు మొదట రంధ్రానికి లంబంగా ఉన్న ఉపరితలాన్ని కొలవవచ్చు, ఆపై ఉపరితలం యొక్క వెక్టార్ దిశను ఆటోమేటిక్ సర్కిల్ (సిలిండర్) కొలత యొక్క వెక్టర్ దిశలో ఇన్పుట్ చేయవచ్చు, రంధ్రం సిద్ధాంతపరంగా లంబంగా ఉందని ఊహిస్తారు. ఉపరితల.లంబంగా కొలిచేటప్పుడు, రంధ్రం యొక్క అక్షం పొడవు మరియు ఉపరితలం మధ్య అనుపాత సంబంధాన్ని అనుభవం ఆధారంగా నిర్ణయించాలి.రంధ్రం లోతు సాపేక్షంగా నిస్సారంగా మరియు ఉపరితలం సాపేక్షంగా పెద్దదిగా ఉంటే మరియు రంధ్రం బెంచ్మార్క్ అయితే, ఫలితం సహనం లేకుండా ఉండవచ్చు (వాస్తవానికి ఇది మంచిది).మీరు రంధ్రంలోకి చొప్పించిన మాండ్రెల్తో కొలవడం లేదా సాధారణ అక్షాన్ని పంచుకునే రెండు రంధ్రాలతో కొలవడాన్ని పరిగణించవచ్చు.
వివిధ రకాల ఖచ్చితత్వ భాగాల CNC మ్యాచింగ్లో GPMకి 20 సంవత్సరాల అనుభవం ఉంది.మేము సెమీకండక్టర్, వైద్య పరికరాలు మొదలైన వాటితో సహా అనేక పరిశ్రమలలో కస్టమర్లతో కలిసి పని చేసాము మరియు కస్టమర్లకు అధిక-నాణ్యత, ఖచ్చితమైన మ్యాచింగ్ సేవలను అందించడానికి కట్టుబడి ఉన్నాము.ప్రతి భాగం కస్టమర్ అంచనాలు మరియు ప్రమాణాలకు అనుగుణంగా ఉండేలా మేము కఠినమైన నాణ్యత నిర్వహణ వ్యవస్థను అనుసరిస్తాము.
కాపీరైట్ నోటీసు:
GPM Intelligent Technology(Guangdong) Co., Ltd. advocates respect and protection of intellectual property rights and indicates the source of articles with clear sources. If you find that there are copyright or other problems in the content of this website, please contact us to deal with it. Contact information: marketing01@gpmcn.com
పోస్ట్ సమయం: మే-27-2024