مشینری مینوفیکچرنگ کے میدان میں، باکس پارٹس ایک عام قسم کے ساختی حصے ہیں اور مختلف مکینیکل آلات میں بڑے پیمانے پر استعمال ہوتے ہیں۔اس کی پیچیدہ ساخت اور اعلی صحت سے متعلق ضروریات کی وجہ سے، باکس حصوں کی پروسیسنگ ٹیکنالوجی خاص طور پر اہم ہے.یہ مضمون جامع اور پیشہ ورانہ طور پر باکس حصوں کی پروسیسنگ ٹیکنالوجی کی وضاحت کرے گا تاکہ قارئین کو متعلقہ علم کو بہتر طور پر سمجھنے اور اس میں مہارت حاصل کرنے میں مدد ملے۔
مواد:
حصہ 1. باکس کے حصوں کی ساختی خصوصیات
حصہ 2. باکس کے حصوں کے لیے پروسیسنگ کی ضروریات
حصہ 3. باکس حصوں کی صحت سے متعلق مشینی
حصہ 4. باکس کے پرزوں کا معائنہ
1. باکس حصوں کی ساختی خصوصیات
پیچیدہ ہندسی شکلیں۔
باکس کے حصے عام طور پر متعدد سطحوں، سوراخوں، سلاٹس اور دیگر ڈھانچے پر مشتمل ہوتے ہیں، اور اندرونی حصہ گہا کی شکل کا ہو سکتا ہے، پتلی اور ناہموار دیواروں کے ساتھ۔اس پیچیدہ ڈھانچے کو باکس کے پرزوں کے ڈیزائن اور مینوفیکچرنگ کے عمل کے دوران بہت سے پہلوؤں کے عین مطابق کنٹرول کی ضرورت ہوتی ہے۔
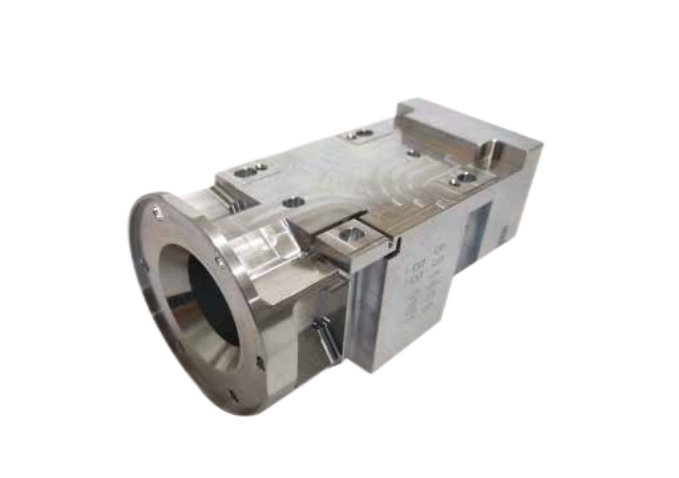
اعلی صحت سے متعلق ضروریات
باکس کے پرزوں کی پروسیسنگ کے لیے نہ صرف ڈیزائن کی ضروریات کو پورا کرنے کے لیے ہر سطح کی ہم آہنگی اور کھڑے ہونے کی ضرورت ہوتی ہے، بلکہ اس میں سوراخوں کی پوزیشن کی درستگی بھی شامل ہوتی ہے۔باکس کے پرزوں کے نارمل آپریشن کو یقینی بنانے کے لیے یہ اہم عوامل ہیں۔
مادی خصوصیات
باکس کے حصوں کے لیے عام طور پر استعمال ہونے والا مواد کاسٹ آئرن یا کاسٹ اسٹیل ہیں۔ان مواد کی کاٹنے کی کارکردگی نسبتاً ناقص ہے، جس سے پروسیسنگ کی دشواری بڑھ جاتی ہے۔
2. باکس حصوں کے لئے پروسیسنگ کی ضروریات
جہتی اور شکل کی درستگی کو یقینی بنائیں
باکس حصوں کی پروسیسنگ کے دوران، سائز اور شکل کی درستگی کو اسمبلی اور استعمال کی ضروریات کو پورا کرنے کے لئے سختی سے کنٹرول کیا جانا چاہئے.
پوزیشن کی درستگی
سوراخوں کی پوزیشن کی درستگی باکس کے حصوں کے لیے خاص طور پر اہم ہے، کیونکہ سوراخ کی پوزیشنوں کی درستگی کا براہ راست تعلق پورے مکینیکل سسٹم کے آپریشن کی درستگی اور استحکام سے ہے۔
سطحی کھردرا
باکس کے حصوں کی رابطے کی سختی اور باہمی پوزیشن کی درستگی کو یقینی بنانے کے لیے، مرکزی طیاروں کی شکل کی درستگی اور سطح کی کھردری کو اعلیٰ معیار تک پہنچنے کی ضرورت ہے۔
فالو اپ پروسیسنگ
خود مشینی کے علاوہ، باکس کے پرزوں کو پروسیسنگ کی تکمیل کے بعد بعد کے علاج کی ایک سیریز سے بھی گزرنا پڑتا ہے، جیسے کہ صفائی، زنگ سے بچاؤ اور پینٹنگ تاکہ ان کے ظاہری معیار اور استحکام کو بہتر بنایا جا سکے۔
باکس حصوں کی صحت سے متعلق مشینی
باکس کے پرزوں کی تکمیل ایک ایسا عمل ہے جس کے لیے انتہائی درستگی کی ضرورت ہوتی ہے، جس کا براہ راست تعلق پورے مکینیکل سسٹم کی اسمبلی کے معیار اور کارکردگی سے ہوتا ہے۔باکس کے حصوں کو ختم کرتے وقت، مندرجہ ذیل مسائل پر خصوصی توجہ دینے کی ضرورت ہے:
مشین اور آلے کا انتخاب
اعلی صحت سے متعلق پروسیسنگ کے نتائج حاصل کرنے کے لئے، اعلی صحت سے متعلق مشینی اوزار اور کاٹنے کے اوزار کا استعمال کرنا ضروری ہے.اس میں اعلی کارکردگی والے آلات جیسے CNC عمودی لیتھز، CNC عمودی مشینی مراکز، اور افقی مشینی مراکز کے ساتھ ساتھ باکس فنشنگ کے لیے وقف اعلیٰ درستگی والے آلات شامل ہیں، لیکن ان تک محدود نہیں ہیں۔
پروسیسنگ پیرامیٹرز کی اصلاح
تکمیل کے عمل کے دوران، پیرامیٹرز جیسے کاٹنے کی رفتار اور فیڈ کی شرح کو درست طریقے سے کنٹرول کرنے کی ضرورت ہے۔پیرامیٹر سیٹنگز جو بہت زیادہ یا بہت کم ہیں پروسیسنگ کوالٹی کو متاثر کر سکتی ہیں، جیسے ضرورت سے زیادہ کاٹنے والی قوتیں پیدا کرنا جو جزوی خرابی کا باعث بنتی ہیں، یا پروسیسنگ کی کارکردگی بہت کم ہے۔
درجہ حرارت اور اخترتی کنٹرول
تکمیل کے عمل کے دوران، طویل مسلسل کاٹنے کے وقت کی وجہ سے، ضرورت سے زیادہ گرم ہونا آسان ہوتا ہے، جس کے نتیجے میں حصے کے غلط طول و عرض یا سطح کا معیار کم ہوتا ہے۔لہٰذا، درجہ حرارت کو کنٹرول کرنے اور تھرمل خرابی کو کم کرنے کے لیے کولنٹ کا استعمال، مناسب طریقے سے پروسیسنگ کی ترتیب اور آرام کے وقت جیسے اقدامات اٹھانے کی ضرورت ہے۔
سوراخ مشینی درستگی
باکس کے پرزوں میں ہول پروسیسنگ ایک ایسا حصہ ہے جس پر خصوصی توجہ کی ضرورت ہوتی ہے، خاص طور پر ان سوراخوں کے لیے جو انتہائی اعلی پوزیشن کی درستگی اور ہم آہنگی کی ضرورت ہوتی ہے۔سوراخوں کی جہتی درستگی اور سطح کے معیار کو یقینی بنانے کے لیے بورنگ، ریمنگ، ریمنگ اور دیگر طریقے استعمال کیے جائیں۔ایک ہی وقت میں، انحراف سے بچنے کے لیے سوراخوں کے درمیان پوزیشنی تعلق پر توجہ دی جانی چاہیے۔
ورک پیس کلیمپنگ کا طریقہ
پروسیسنگ کی درستگی کو یقینی بنانے کے لیے کلیمپنگ کا درست طریقہ بہت ضروری ہے۔پروسیسنگ کے دوران ورک پیس کے استحکام کو یقینی بنانے اور غلط کلیمپنگ کی وجہ سے پروسیسنگ کی غلطیوں سے بچنے کے لیے مناسب ٹولنگ کو ڈیزائن کیا جانا چاہیے۔مثال کے طور پر، ٹرانزیشنل تھریڈڈ ہولز کا طریقہ استعمال کرتے ہوئے بڑی سطحوں کی گھسائی اور ڈرلنگ کو ایک ہی کلیمپنگ میں مکمل کیا جا سکتا ہے، جس سے چپٹا پن کو مؤثر طریقے سے بہتر کیا جا سکتا ہے۔
4. باکس حصوں کا معائنہ
باکس کے پرزوں کا معائنہ اس بات کو یقینی بنانے کے لیے ایک اہم قدم ہے کہ وہ مکینیکل سسٹم کی درستگی اور کارکردگی کی ضروریات کو پورا کرتے ہیں۔معائنہ کے عمل کے دوران، بہت سی تفصیلات پر توجہ دینے کی ضرورت ہے۔
پیمائش کے اوزار
اعلی درستگی کی پیمائش کے نتائج حاصل کرنے کے لیے، یہ ضروری ہے کہ اعلی استحکام اور اعلی کارکردگی کی پیمائش کے اوزار، جیسے کہ سہ جہتی کوآرڈینیٹ ماپنے والی مشینیں استعمال کریں۔یہ آلات باکس کے پرزوں کے طول و عرض، ہمواری، ہم آہنگی وغیرہ کی قطعی پیمائش کا ایک سلسلہ حاصل کر سکتے ہیں۔
پیمائش کے لوازمات کو ترتیب دیں۔
گہرے سوراخوں اور گہاوں میں پیمائش کے لیے پیمائش کی درستگی کو یقینی بنانے کے لیے مناسب ایکسٹینشن راڈز اور اسٹائل کی ضرورت ہوتی ہے، جیسے ٹیسٹ بیس ایکسٹینشن راڈ، ستارے کی شکل والی اسٹائلی وغیرہ۔
پوزیشننگ کا تعین کریں۔
پیمائش کرنے سے پہلے، باکس کے حصوں کی پوزیشننگ کے طریقہ کار کو واضح کرنا ضروری ہے.عام طور پر پوزیشننگ کے لیے تین باہمی طور پر کھڑی سطحیں یا ایک طیارہ جس میں پوزیشننگ کے لیے دو کھڑے سوراخ ہوتے ہیں۔یہ پیمائش کی تکرار اور استحکام کو بہتر بنانے میں مدد کرتا ہے۔
بڑھتے ہوئے طریقوں پر غور کریں۔
اس بات کو مدنظر رکھتے ہوئے کہ باکس کے پرزے سائز میں نسبتاً بڑے اور وزن میں بھاری ہوتے ہیں، کلیمپنگ کے وقت سہولت، تکرار اور استحکام کو یقینی بنایا جانا چاہیے۔انہیں پیمائش کے لیے کام کی سطح پر براہ راست رکھا جا سکتا ہے، یا یونیورسل کلیمپس یا سادہ کلیمپس کا استعمال کرتے ہوئے انہیں ٹھیک کیا جا سکتا ہے۔
احتیاطی تدابیر پر عمل کریں۔
پیمائش کرتے وقت، آپ کو اس بات کو یقینی بنانا چاہیے کہ پرزے صاف اور گڑھوں سے پاک ہیں، پیمائش کے عناصر کی سطح کی درستگی کو زیادہ رکھیں، اور پرزوں کی غلط حرکت سے بچنے کے لیے پیمائش کی مناسب رفتار کا انتخاب کریں، خاص طور پر جب بہت سے سائز ہوں۔ایک ہی وقت میں، ایسے مقامات کے لیے جن کی براہ راست پیمائش کرنا مشکل ہے، متعدد کلیمپنگ یا بالواسطہ پیمائش کے طریقوں پر غور کیا جا سکتا ہے۔
پیمائش کے ڈیٹا کا تجزیہ کریں۔
ناپے گئے ڈیٹا کا بغور تجزیہ کرنے کی ضرورت ہے، خاص طور پر کلیدی پیرامیٹرز جیسے سوراخ کی جہتی درستگی، سلنڈریت، اور سماکشی، جس کا تجزیہ پیمائش کے نتائج کی درستگی اور وشوسنییتا کو یقینی بنانے کے لیے پروسیسنگ اور اسمبلی کی اصل حالتوں کے ساتھ مل کر کیا جانا چاہیے۔
پیمائش کی مہارت کی تصدیق کریں۔
سوراخ کے محور کی پیمائش کرتے وقت، آپ سب سے پہلے اس سطح کی پیمائش کر سکتے ہیں جو سوراخ پر کھڑا ہے، اور پھر سطح کی سمتیہ کی سمت کو خودکار دائرے (سلنڈر) کی پیمائش کی سمتیہ سمت میں داخل کریں، یہ فرض کرتے ہوئے کہ سوراخ نظریاتی طور پر کھڑا ہے سطح۔کھڑے ہونے کی پیمائش کرتے وقت، سوراخ کے محور کی لمبائی اور سطح کے درمیان متناسب تعلق کو تجربہ کی بنیاد پر پرکھنا ضروری ہے۔اگر سوراخ کی گہرائی نسبتاً کم ہے اور سطح نسبتاً بڑی ہے، اور سوراخ بینچ مارک ہے، تو نتیجہ برداشت سے باہر ہو سکتا ہے (دراصل یہ اچھا ہے)۔آپ سوراخ میں ڈالے گئے مینڈرل سے پیمائش کرنے یا مشترکہ محور والے دو سوراخوں کے ساتھ پیمائش کرنے پر غور کر سکتے ہیں۔
GPM کے پاس مختلف قسم کے صحت سے متعلق حصوں کی CNC مشینی میں 20 سال کا تجربہ ہے۔ہم نے سیمی کنڈکٹر، طبی آلات وغیرہ سمیت کئی صنعتوں میں صارفین کے ساتھ کام کیا ہے، اور صارفین کو اعلیٰ معیار کی، درست مشینی خدمات فراہم کرنے کے لیے پرعزم ہیں۔ہم ایک سخت کوالٹی مینجمنٹ سسٹم اپناتے ہیں تاکہ یہ یقینی بنایا جا سکے کہ ہر حصہ کسٹمر کی توقعات اور معیارات پر پورا اترتا ہے۔
کاپی رائٹ نوٹس:
GPM Intelligent Technology(Guangdong) Co., Ltd. advocates respect and protection of intellectual property rights and indicates the source of articles with clear sources. If you find that there are copyright or other problems in the content of this website, please contact us to deal with it. Contact information: marketing01@gpmcn.com
پوسٹ ٹائم: مئی 27-2024